The Central Economic Work Conference clearly pointed out that we should adhere to the principle of stability and seek progress while maintaining stability, stressed the strengthening of various policy coordination and cooperation, and made a series of deployments such as “accelerating the construction of a modern industrial system”, “focusing on strengthening weak links in the industrial chain” and “vigorously developing the digital economy”.
The year 2023 is the first year to fully implement the spirit of the Party’s 20 National Congress, and it is of great significance to do economic work well. How to promote steady industrial growth? How to enhance the core competitiveness of manufacturing industry? Minister of Industry and Information Technology Jin Zhuanglong recently accepted an interview with Xinhua News Agency
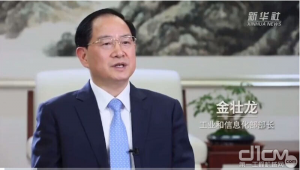
We have the confidence, conditions and ability to promote the steady recovery of the industrial economy
Q: What was the performance of the industrial economy in the past year? How to promote stable industrial growth in 2023?
A: Over the past year, we have worked with various regions and departments to actively respond to the impact of unexpected factors, implement a package of policies to stabilize the economy, and promptly introduce a series of measures to boost the industrial economy. From January to November 2022, China’s industrial added value above designated size increased by 3.8% year-on-year, continuing to play the role of “ballast” for industrial stability of the macroeconomic market.
It is undeniable that the operation of the industrial economy still faces difficulties and challenges, but it should be noted that the advantages of a complete industrial system and a strong domestic market are prominent. In 2023, the combination of optimized epidemic prevention and control measures, stock policies and incremental policies will greatly boost market confidence. We have the confidence, conditions and ability to promote the steady recovery of the industrial economy.
The Ministry of Industry and Information Technology will increase efforts to stabilize growth, strengthen the coordination and cooperation of various policies, and focus on four aspects of work:
First, we strengthened the supply and implementation of policies to stabilize growth. Strengthen the coordination of departments and the linkage of ministries and provinces, implement the policies and follow-up measures that have been issued, strengthen the monitoring and scheduling of industrial economic operation, situation research and judgment, and policy reserves, and introduce more policies and measures in a timely manner.
Second, focus on key industries and regions to stabilize the basic plate of industrial growth. For pillar industries such as machinery, petrochemicals, light industry, automobiles, and electronics, we will study and formulate measures to stabilize growth on a section-by-sector basis. We will create more new growth areas for emerging industries such as new energy, new materials, next-generation information technology, and high-end equipment. We will support the major industrial provinces in taking up the leading role, and support all regions in leveraging their respective strengths and achieving their growth targets.
Third, fully implement the “14th Five-Year Plan” series of plans to boost effective investment in manufacturing. For identified major projects, major projects, major projects, and major projects, start implementation as soon as possible to form a physical workload. We will support manufacturing enterprises to increase investment in high-end, intelligent, and green development, and strengthen service guarantees for major foreign-invested projects in the manufacturing industry.
Fourth, we will actively expand consumption and create new demand with high-quality supply. We will implement the project of new energy vehicles leading the way and developing a strong foundation, and carry out trials for access to intelligent and connected vehicles. We will further implement the “Increase variety, improve quality, and create brands” campaign, promote the movement of green smart home appliances and green building materials to the countryside, vigorously cultivate demonstration cities for information consumption, and promote the development of new technologies, new products, and new models.
Forging long boards, reinforcing short boards, strengthening foundations, and comprehensively upgrading the modernization level of the industrial system
Q: The Central Economic Work Conference emphasized speeding up the construction of a modern industrial system. What specific measures will the Ministry of Industry and Information Technology take?
A: To build a modern industrial system, the key lies in revitalizing the manufacturing industry. We will forge long boards, strengthen weak boards, strengthen the foundation, and comprehensively modernize the industrial system. We will focus on the following five areas:
First, we will improve the autonomy and controllability of key industrial chains. We will identify the weak links in key core technologies and components, carry out key core technology research projects, improve market mechanisms such as “revealing-list”, and take solid steps to strengthen chains and stabilize chains. We will pool high-quality resources to tackle key problems.
Second, we will deepen the reconstruction of the industrial base. Focusing on core basic components, core basic components, key basic materials, key basic software, advanced basic processes and industrial technology foundations, vigorously implementing industrial basic reconstruction projects, laying out a number of common industrial basic technology centers in key areas, and cultivating a number of national manufacturing innovation centers, and actively giving play to the role of key laboratories. Strive to break through a number of key urgently needed basic products.
Third, we will consolidate our leading position in competitive industries. We will accelerate the construction of new infrastructure such as 5G, deepen the integrated application of “5G+ Industrial Internet”, and promote the research and development of 6G technology. Strengthen the new energy automobile industry, comprehensively enhance the competitiveness of the photovoltaic industry, and promote the high-quality development of the shipbuilding industry.
Fourth, we will vigorously transform and upgrade traditional industries. Cultivate a group of leading enterprises with resource control and international competitiveness, vigorously promote technological transformation and equipment upgrading of enterprises, in-depth implementation of intelligent manufacturing projects, comprehensive implementation of green manufacturing, and forge new industrial competitive advantages.
Fifth, we will accelerate the cultivation and growth of emerging industries. We will accelerate the innovation and development of strategic emerging industries such as artificial intelligence, biofuturing, and the Internet of Things, implement special actions for the development of advanced manufacturing clusters, study and formulate action plans for future industrial development, and accelerate the planning and layout of future industries such as humanoid robots, meta-universe, and quantum technology.
We will step up rescue assistance to stabilize market expectations and boost business confidence
Q: In 2023, what new measures will be taken to help enterprises rescue, and how will expectations be stabilized and confidence strengthened?
A: In response to many unexpected factors, China promptly introduced a series of policy measures to relieve difficulties. With the support of various pro-enterprise policies, the majority of small and medium-sized enterprises have been constantly striving to overcome difficulties, showing strong resilience and vitality.
At present, the difficulties and challenges of the stable development of small and medium-sized enterprises are still relatively large, and the Ministry of Industry and Information Technology will further strengthen the policy of benefiting enterprises, the environment of enterprises, the service of enterprises, the innovation of enterprises, and the talent of enterprises, and make every effort to promote the high-quality development of small and medium-sized enterprises.
Specifically, it includes continuously optimizing the development environment, improving the regulations and policies system for small and medium-sized enterprises, continuously carrying out environmental assessment and comprehensive supervision of small and medium-sized enterprises development, and carrying out special actions to reduce the burden on enterprises. We will increase assistance and support, coordinate and promote the continuation and improvement of phased pro-business policies, and introduce a number of measures to help micro, small and medium-sized enterprises maintain steady growth, adjust their structure, and strengthen their capabilities. We will promote the development of specialized and specialized new enterprises, and strive to have more than 80,000 specialized and specialized new small and medium-sized enterprises and more than 10,000 “small giant” enterprises nationwide by the end of 2023. Build a high-quality and efficient service system, and improve the service system for small and medium-sized enterprises at the national, provincial, city and county levels; We will strengthen international exchanges and cooperation, build a number of cooperation zones for small and medium-sized enterprises, improve the overseas service system for small and medium-sized enterprises, and help them “go global”.
We will consolidate the foundation and expand applications, and accelerate the integration of the digital economy and the real economy
Q: What specific measures will the Ministry of Industry and Information Technology take to vigorously develop the digital economy?
A: The digital economy is an important engine driving China’s economic growth and an important advantage in building a modern industrial system. China has built the world’s largest and most technologically advanced network infrastructure, with 2.28 million 5G base stations and gigabit optical networks capable of covering 500 million households. The industrial Internet has been widely integrated into 45 national economic categories, and the role of the digital economy in empowering the real economy has become increasingly prominent.
In 2023, we will thoroughly implement the decisions and arrangements of the Party Central Committee and The State Council, focus on digital technology innovation breakthroughs and application expansion, and promote the deep integration of the digital economy and the real economy.
First, accelerate the construction of digital infrastructure. We will deepen the construction of 5G and gigabit optical networks, coordinate the construction of new infrastructure such as data centers and the industrial Internet, and accelerate the deployment and application of the Internet of vehicles. We will carry out the “Broadband Frontier” special action, and give strong support to the construction of “double gigabit” networks in areas with demand and conditions.
Second, we will promote the innovative development of the digital industry. Focus on key areas such as integrated circuits, 5G, and new displays, and improve the supply of basic hardware and software, core electronic components, key basic materials, and intelligent manufacturing equipment. We will study and formulate supporting policies to better leverage the role of data factors and build world-class digital industrial clusters.
Third, we will deepen industrial digital transformation. Carry out digital transformation actions in the manufacturing industry, promote the popularization of the industrial Internet to industrial parks, build a number of 5G fully connected factories, build a number of global leading smart factories and smart supply chains, and promote the scenario and standardization of small and medium-sized enterprises.
Fourth, we will strengthen network and data security. We will strengthen capacity building for security protection of network infrastructure, establish norms and standards for data security in the industrial and information technology fields, and enhance security capabilities in new convergence areas such as 5G, the industrial Internet, and the Internet of vehicles.
Fifth, improve the environment for the development of the digital economy. Innovate telecom market supervision, guide and urge the compliance development of platform enterprises, deepen the comprehensive management of the network environment such as preventing and cracking down on telecom network fraud, and comprehensively strengthen the protection of users’ rights and interests.
3800mm wide and thick plate production line, hot test success!
At 8:58 am on December 16, 2024, the 3800mm roughing mill of West China Special Steel Wide and Thick plate began rolling. After finishing rolling, straightening, cooling and other processes, the first qualified steel plate was born! The whole production process is stable, the steel plate size accuracy is high, the plate shape is straight, and the surface quality is good, which indicates that the thermal load test has been a complete success!
Since the start of the project on December 15, 2023, the company’s leaders have attached great importance to the project, the project command department has been carefully organized and scientifically deployed, and the construction units and factory employees have overcome difficulties and worked together to promote the rapid progress of the project in terms of quality and quantity. The hot test plan is thorough and complete, the prenatal training of the operators is comprehensive and meticulous, and the wide and thick plate project is forced to meet the hot test conditions on schedule, and a hot test is successful.
The 3800mm wide and thick plate production line of Huaxi Special Steel adopts two-stand high-stiffness four-high rolling mill, and the basic automation and process automation system adopts the world-leading PRIMETALS technology to ensure the thickness and width accuracy of the products. The strong pre-straightener and the hot straightener create conditions for the production of wide and thick plates with good flatness; Online ultrasonic automatic flaw detection equipment to ensure that the internal quality of products is good. Designed annual output of 2 million tons, the variety covers high-rise building structural steel, welding structural steel, bridge structural steel, weather resistant structural steel, ship and ocean engineering structural steel, boiler and pressure vessel steel, pipeline steel plate, automobile girder steel plate, high strength wear-resistant steel plate for construction machinery, etc. The product specifications are: thickness 6mm ~ 200mm; Width 1600 ~ 3650mm; The length ranges from 6000mm to 18000mm.
The success of the hot test marks that Huaxi Special Steel has practiced the group’s strategy of developing steel varieties, improved the product structure of Huaxi Special Steel, realized the complete industrial chain of iron, steel and materials, and enhanced the core competitiveness of the enterprise in the market, which is another milestone in the history of Huaxi Special Steel! Standing at a new historical starting point, Huaxi Special Steel will uphold the group’s “pragmatic and truth-seeking, always strive for the first” spirit of enterprise, lead the high-quality development of enterprises with high-tech applications, and create a green, low-carbon, advanced technology and the most competitive modern special wide and thick plate quality base
Where are forgings used in various industries?
Core Tip: During the use of forgings, the process requirements are very strict, and each piece needs to be consistent without any porosity, excess space, inclusions, or other defects. Components produced by this method.
During the use of forgings, the process requirements are very strict, requiring each piece to be consistent, without any porosity, excess space, inclusions, or other defects. The components produced by this method have a high ratio of strength to weight. These components are typically used in aircraft structures. Of course, this does not mean that these forgings are not allowed to be used in other industries. Obviously, forgings are widely used in various industries of industrial production.
1、 Aircraft forgings: Approximately 85% of the components on an aircraft are forgings by weight. The turbine discs, rear axle necks (hollow shafts), blades, wing beams of aircraft engines, rib plates and wheel supports of the fuselage, and inner and outer cylinders of landing gear are all important forgings related to aircraft safety.
2、 Diesel engine forgings: Diesel engines are a type of power machinery commonly used as engines. Taking a large diesel engine as an example, there are more than ten types of forgings used, including cylinder head, main journal, crankshaft end flange output shaft, connecting rod, piston rod, piston head, crosshead pin shaft, crankshaft transmission gear, ring gear, intermediate gear, and dye pump body.
3、 Marine forgings: Marine forgings are divided into three categories: main engine forgings, shaft forgings, and rudder forgings. The main engine forging is the same as the diesel engine forging. Shaft forgings include thrust shafts, intermediate shafts, and stern shafts. Rudder forgings include rudder stock, rudder column, rudder pin, etc.
4、 Weapon forgings: Forgings play an extremely important role in the weapon industry. By weight, 60% of tanks are made up of forgings. The barrel, muzzle brake, and tail of artillery, rifled barrels and triangular bayonets in infantry weapons, rocket and submarine depth charge launchers and mounts, stainless steel valve bodies for high-pressure coolers in nuclear submarines, shells, bullets, etc. are all forged products. Besides steel forgings, weapons are also made from other materials.
5、 Petrochemical forgings: Forgings have a wide range of applications in petrochemical equipment. Manholes and flanges for spherical storage tanks, various tube plates and welded flanges required for heat exchangers, forged cylinder bodies (pressure vessels) for catalytic cracking reactors, cylinder sections used for hydrogenation reactors, and top covers, bottom covers, and heads required for fertilizer equipment are all forged parts.
6、 Mining forgings: Calculated by equipment weight, the proportion of forgings in mining equipment is 12-24%. Mining equipment includes mining equipment, hoisting equipment, crushing equipment, grinding equipment, washing equipment, and sintering equipment.
7、 Nuclear power forgings: Nuclear power is divided into two categories: pressurized water reactors and boiling water reactors. The main large forgings of nuclear power plants can be divided into two categories: pressure shells and reactor internals. The pressure shell includes: cylinder flange, nozzle section, nozzle, upper cylinder, lower cylinder, cylinder transition section, bolts, etc. The internal components of the reactor work under severe conditions such as high temperature, high pressure, strong neutron irradiation, boric acid water corrosion, erosion, and hydraulic vibration, so 18-8 austenitic stainless steel should be selected for production.
8、 Thermal power forgings: There are four key forgings in thermal power equipment, namely the rotor and retaining ring of the steam turbine generator, as well as the impeller and rotor in the steam turbine.
9、Hydroelectric forgings: Important forgings in hydroelectric power station equipment include turbine shaft, turbine generator shaft, mirror plate, thrust head, etc.
What Is the Forgings for Coke Oven Vehicle Equipment?
Forgings for coke oven vehicle equipment usually include various connecting parts, supporting parts, transmission parts and structural parts. These forging parts need to have good mechanical properties and high temperature and corrosion resistance to adapt to the harsh working environment in the coke oven. The material of forged parts is generally selected as high-strength alloy steel or special steel to ensure its stability and reliability under high temperature and heavy load. Common forging parts are wheels, shafts, gears, bearing seats, connecting rods, hooks and so on. In the design and manufacture of these forging parts, it is necessary to strictly comply with the relevant industry standards and specifications to ensure that the quality and performance of the product meet the requirements of the use of coke oven vehicle equipment.
In addition, forgings for coke oven vehicle equipment in the production process, but also need to go through multiple processes of fine processing and heat treatment to improve its internal organization and mechanical properties. This includes forging, heat treatment, machining, surface treatment and other key links. Forging is the process of molding metal materials into the desired shape by applying pressure, which can eliminate the defects inside the material and improve the density and mechanical properties of the material. Heat treatment, including quenching, tempering and other processes, is designed to further improve the hardness and toughness of the forged parts, so that it can better adapt to high temperature and heavy load working conditions.
Machining is the process of machining the forged parts to the exact size and shape, which includes turning, milling, grinding and other processing methods. Surface treatment is mainly to enhance the corrosion resistance and beauty of forged parts, the common surface treatment methods are sandblasting, painting, electroplating and so on. In terms of quality control, forged parts for coke oven vehicle equipment need to undergo strict inspection and testing, including appearance inspection, dimensional measurement, non-destructive testing, mechanical properties testing, etc., to ensure that each product meets the relevant standards and requirements. In short, the forging parts for coke oven vehicle equipment are the key parts in coke oven production, and their quality and performance are directly related to the stability and reliability of coke oven vehicle equipment. Therefore, in the design and manufacturing process, it is necessary to fully consider its working environment and use requirements to ensure that the quality and performance of the product reach the best state.
2024 National Mechanical Industry High-Quality Development Conference Held in Hangzhou
On December 11, 2024, the 2024 National Mechanical Industry High-Quality Development Conference, themed “Upholding Integrity, Innovating for a Better Future,” was held in Hangzhou. The event also marked the awarding ceremony of the third “Hangyang Cup” National Mechanical Industry Product Quality Innovation Contest. The conference was jointly hosted by the China Machinery Industry Federation and China National Machinery Industry Corporation.
Keynote speeches were delivered by prominent leaders, including Luo Junjie, member of the Standing Committee of the Party Committee and Executive Vice President of the China Machinery Industry Federation; Shen Kaibo, Deputy Secretary-General of the Hangzhou Municipal People’s Government; Yao Jianzhong, Second-level Inspector of the Zhejiang Provincial Department of Economy and Information Technology; Gan Xiaobin, Deputy Director of the Science and Technology Department of the Ministry of Industry and Information Technology; and Wang Jun, Deputy Director of the Product Quality and Safety Supervision Administration of the State Administration for Market Regulation.
In his speech, Luo Junjie highlighted the remarkable achievements of the mechanical industry in recent years, particularly in four key areas: stable growth in industrial scale and economic indicators, breakthroughs in innovation-driven major equipment, accelerated development of strategic emerging industries, and the emergence of strong competitive brands and enterprises with high market recognition.
However, Luo also warned of challenges ahead. In the face of global uncertainties and the impact of international markets and geopolitical shifts, the mechanical industry still grapples with issues such as overcapacity in low-end products, price competition, insufficient high-end supply, weak industry foundations, and limited innovation capabilities. He urged the industry to recognize these challenges and adopt a sense of urgency, continue fostering confidence, and strive toward achieving high-quality development.
Luo outlined five key suggestions for the future development of the industry:
The event also featured thematic reports from Chen Xuedong, Vice General Manager of China National Machinery Industry Corporation and an academician of the Chinese Academy of Engineering, as well as Tan Jianrong, academician of the Chinese Academy of Engineering. Chen discussed enhancing industry foundation capabilities and promoting high-quality development, while Tan addressed the role of new production power and digital transformation.
In addition, experts such as Zheng Wei, Chairman of Hangyang Group Co., Ltd., Luo Kai, Co-President of Zoomlion Heavy Industry Science and Technology Co., Ltd., and Wang Tairan, Chief Expert of Quality Management Digitalization at the China Academy of Information and Communications Technology, delivered speeches covering product innovation, operational management, corporate culture, and talent development.
The “Hangyang Cup” Third National Mechanical Industry Product Quality Innovation Contest was met with enthusiastic participation from the industry. A total of 241 projects won awards, including 30 gold medals, 100 silver medals, and 111 excellent awards. One unit received a special contribution award. During the conference, representatives of award-winning enterprises visited Hangyang Group Co., Ltd., Hangcha Group Co., Ltd., and Zhejiang Wanma Co., Ltd. for research and exchange.
This conference serves as a key milestone in the ongoing efforts to advance the mechanical industry’s transformation toward high-quality development, focusing on technological innovation, sustainability, and the cultivation of competitive enterprises.
The country’s first, was born in Qinghai music capital!
On December 2, the reporter learned from the Ledu Industrial Park of Haidong City that Qinghai Middle Titanium Blue Forging Equipment Manufacturing Co., LTD. (hereinafter referred to as “Middle Titanium Blue Forging”) in the Ledu Industrial Park of Haidong Industrial Park continued to promote technological innovation and successfully produced the country’s first new high-temperature alloy large diameter thin-wall pipe for 650℃ grade power stations. This breakthrough marks China’s major progress in the field of high-temperature alloy pipes for power stations, which not only fills the relevant technical gaps in China, but also has far-reaching significance for the high-end equipment manufacturing of China’s power industry.
China Titanium Blue Forging successfully overcome the problems of narrow hot processing window of superalloy, difficult structure and property control, complex extrusion process design, etc., successfully produced the first new superalloy (GH2070P) large-diameter thin-wall pipe for 650℃ grade power station in China on the 680MN extrusion machine, with an outer diameter of 610mm, wall thickness of 30mm, and length of more than 6.4m. It is reported that during the trial production process, titanium blue forging gives full play to the technical advantages of the industry, from the precise selection and ratio of raw materials, to the optimization and innovation of the forging process, to the fine control of heat treatment and subsequent processing processes, each link has undergone rigorous research and development and repeated trials. In the meantime, advanced forging equipment and precision testing instruments are used to ensure that the dimensional accuracy of the pipe, internal organizational performance and other indicators are in line with high standards.
“High combination 2070p superalloy pipe is a new type of power station pipe, this material due to its superb deformation resistance, making the molding difficult, the thick wall pipe used by each power station before, resulting in very high power station operation costs.” Through technological optimization and innovation, we have successfully produced the first ultra-thin-wall high-tech pipeline in China, which can greatly reduce the cost of power stations and has certain significance for promoting the realization of the dual-carbon goal in China.” Du Hongqiang, vice general manager of China Titanium blue forging, said.
It is reported that in recent years, China Titanium blue forging has a complete production and manufacturing system such as preforming, forging, hot extrusion/die forging, heat treatment, processing, testing, etc. The key equipment 680MN/260MN unit is the world’s first dual-function heavy equipment that integrates hot extrusion and die forging independently designed and built in China, and the hot extrusion capacity ranks first in the world.
Henan: Strengthen graphene research and development and industrial application to accelerate the construction of strong materials province
On November 28, the opening ceremony of Zhongyuan Graphene Laboratory was held in the Aviation Port area.
On November 28, the opening ceremony of Zhongyuan Graphene Laboratory was held in the Aviation Port area. Henan Provincial Party Secretary Lou Yangsheng attended and delivered a speech, and Henan Provincial Governor Wang Kai attended.
Lou Yangsheng unveiled the Zhongyuan Graphene Laboratory, and Wang Kai awarded the appointment letter of director of Zhongyuan Graphene Laboratory to Liu Zhongfan, academician of the Chinese Academy of Sciences. Liu Zhongfan introduced the general situation and development concept of the laboratory.
On behalf of the provincial Party Committee and the provincial government, Lou Yangsheng congratulated the establishment of the laboratory, and thanked the Central Committee of the Jiusan Society and academician experts for their concern and support for the development of Henan. He said that the opening of the Zhongyuan Graphene laboratory is of great significance for Henan Province to strengthen the research and development and industrial application of graphene and build a strong province of materials. A major feature of the establishment of the Zhongyuan Graphene Laboratory is to simultaneously land Zhongyuan ene Carbon Co., LTD., Zhongyuan ene carbon Industry Fund, to build a trinity of “science and technology + industry + capital” industrial innovation closed loop, with the laboratory as the “foundation”, industrial companies as the “backbone”, and incubation projects as the “branches and leaves”, to cultivate a competitive and leafy Zhongyuan graphene industry tree. It is hoped that Zhongyuan Graphene Laboratory will live up to its trust and fulfill its mission, take innovation and creation as the starting point and the product industry as the starting point, combine science and technology and industry more closely, and strive to become a strategic scientific and technological force in the field of graphene materials and an important supporting force for the construction of a strong province of Henan materials.
Lou Yangsheng stressed that the Central Plains Graphene Laboratory should focus on the world’s scientific and technological frontier, the major national needs and the development needs of our province, carry out application scenario research and engineering verification, and strive to break through the key common technologies for the large-scale preparation of graphene materials, forming a number of landmark innovation achievements and typical applications. It is necessary to systematically sort out and integrate high-quality research and development resources, educational resources, and industrial resources, strengthen collaborative innovation, strengthen organized, systematic, and full-link technology research capabilities, and accelerate the solution of technical and process problems in the field of graphene materials. It is necessary to improve the result transfer and transformation, venture capital service system, through the graphene industrial chain, innovation chain, capital chain, improve the service capacity of the whole chain, and promote the graphene industry to become bigger and stronger. It is necessary to build a bridge linking “material” and “market”, and build a demonstration application industry chain of graphene materials in combination with the industrial advantages of new energy vehicles, consumer electronics manufacturing, and wind power new energy in Henan Province. It is necessary to thoroughly study and grasp the law of scientific research activities and the law of talent growth, optimize the mode of operation and the paradigm of scientific research, improve the flexible market-oriented mechanism for attracting and cultivating talents, and build a dynamic new type of research and development institutions, so as to make contributions to promoting the self-reliance and self-improvement of high-level science and technology.
Us Export Control to China! China’s Four Major Associations Voice: Cautious Purchase of American Chips
On December 2, the US government announced a new round of export restrictions on China, adding more than 140 Chinese enterprises to the list of trade restrictions, involving semiconductor manufacturing equipment, electronic design automation tools and other types of semiconductor products. In this regard, on the evening of December 3, the China Semiconductor Industry Association, the China Association of Automobile Manufacturers, the Internet Association of China, and the China Association of Communications Enterprises successively issued a statement saying that they recommended that relevant industries in China carefully purchase U.S. chips.
China Semiconductor Industry Association: China’s relevant industries will have to be cautious about purchasing U.S. chips
The China Semiconductor Industry Association believes that the U.S. government’s behavior has once again destroyed the global semiconductor industry’s long-standing consensus on fairness, rationality, and non-discrimination, as well as the purpose of WTO fair trade, and violated the spirit of the World Semiconductor Council (WSC) charter, which is followed by global semiconductor companies, and hurt the efforts of global semiconductor practitioners to unite and cooperate.
“The US government’s arbitrary revision of trade rules has caused substantial damage to the security and stability of the global semiconductor industry chain.” The China Semiconductor Industry Association said that in today’s global economic integration, the unilateralism of the US government has not only damaged the interests of Chinese and American enterprises, but also greatly increased the cost of the global semiconductor supply chain. As the US export control measures continue to increase, their counter-biting effect is also continuing to expand. The arbitrariness of the United States’ control measures on China has also caused supply chain disruptions and rising operating costs for American companies, affecting the stable supply of chips in the United States.
The China Semiconductor Industry Association believes that American chips are no longer safe and reliable, and relevant industries in China will have to carefully purchase American chips. The development of China’s semiconductor industry is rooted in globalization, growth and expansion in globalization. “We will always adhere to open cooperation, actively deepen cooperation with upstream and downstream semiconductor companies in various countries, and promote the prosperity of the global industry,” the China Semiconductor Industry Association said.
The China Semiconductor Industry Association said that it strongly urges the US government to respect the consensus of the industry, return to the spirit of the WSC charter, safeguard the common interests of the global semiconductor industry, and shoulder the responsibility and responsibility of a major country.
The China Semiconductor Industry Association will maintain the fairness principle and industry consensus formed by WSC, resolutely defend the interests of Chinese semiconductor enterprises and global supply chain partners, and call on enterprises in relevant countries and regions to strive to become reliable semiconductor product suppliers, and also call on the Chinese government to support the stable development of reliable semiconductor product suppliers.
China Association of Automobile Manufacturers: American car chips are no longer reliable and safe
The China Association of Automobile Manufacturers issued a statement saying that it resolutely opposes the US government’s generalization of the concept of national security, abuse of export control measures, and malicious blockade and suppression of China. Such acts seriously violate the laws of the market economy and the principle of fair competition, undermine the international economic and trade order, disrupt the stability of the global industrial chain, and ultimately harm the interests of all countries. “In order to ensure the safety and stability of the auto industry chain and supply chain, the association recommends that Chinese auto companies carefully purchase U.S. chips.”
The China Association of Automobile Manufacturers said that the US government’s arbitrary modification of the control rules has seriously affected the stable supply of US chips, and the trust and confidence of the Chinese auto industry in the purchase of chips from US companies is being shaken, and US auto chips are no longer reliable and safe. Automobile is a highly global industry, and China’s automobile industry has always been rooted in the development of globalization. China’s automobile industry is in a stage of rapid development, especially the rapid development of new energy vehicles, which has become an important driving force for global green and low-carbon transformation, and also provides a broad market space for the global automobile industry chain.
The China Association of Automobile Manufacturers said that it welcomes global chip companies to strengthen cooperation with Chinese auto and chip companies in various aspects, invest in China, jointly research and development, and share development opportunities.
Internet Society of China: Seek to expand cooperation with chip companies in other countries and regions
The Internet Society of China issued a statement saying that in order to ensure the safety, stability and sustainable development of China’s Internet industry, it called on domestic enterprises to take the initiative to take countermeasures, prudentially choose to purchase chips from the United States, seek to expand cooperation with chip companies in other countries and regions, and actively use chips manufactured by domestic and foreign enterprises in China.
The Internet Society of China believes that the United States has frequently adjusted control rules, continuously upgraded trade barriers, and ignored international trade rules, which has caused substantial damage to the healthy and stable development of China’s Internet industry.
The Internet Society of China pointed out that the United States has generalized the concept of national security and abused export control means to block and suppress China, which has shaken the industry’s trust and confidence in American chips.
The Internet Society of China said that while the United States ignores the stability and security of the global supply chain, China should still insist on expanding its independent opening up. On the basis of ensuring security, we will continue to firmly establish and maintain cooperative and win-win relations with all parties in the world and promote the prosperity and development of the global economy. In the critical period of the information technology revolution, China should join hands with all sectors of the world to scale the technological peak and jointly build a better digital future.
The Difference Between Forging Crane Wheel Forging And Driving Wheel Forging
The difference between forging crane wheel forgings and driving wheel forgings mainly lies in their application, size, carrying capacity and design requirements. Forging crane wheel forgings are usually used in large bridge cranes and gantry cranes, which need to bear larger loads and are larger in size and are designed to require higher strength and durability. The driving wheel forgings are mostly used for small light cranes or driving, they carry relatively small weight, the size is also small, the design of the strength and durability requirements are relatively low. In addition, the two may also differ in the manufacturing process to accommodate different performance needs and cost considerations.
In addition, forging crane wheel forgings and driving wheel forgings may also differ in material selection. Since crane wheel forgings need to withstand greater weight and stress, materials with higher strength and wear resistance are usually selected to ensure their long-term stable operation. The driving wheel forging may use more ordinary materials, because the load it bears is small, and the requirements for material properties are relatively low.
In terms of service life, forging crane wheel forgings are often in a state of high load operation, and their service life may be relatively short, requiring regular inspection and maintenance. The service life of wheel forgings may be relatively long because their operating conditions are relatively mild.
In short, forging crane wheel forgings and driving wheel forgings are different in many aspects, and these differences make them suitable for different crane and driving scenarios. When choosing wheel forgings, it is necessary to comprehensively consider the specific application, load requirements, cost budget and other factors to ensure that the selected forgings can meet the actual needs and have a good cost performance.
Go all out to stabilize the industry, solid forging new advantages! Visit Minister of Industry and Information Technology Jin Zhuanglong
The Central Economic Work Conference clearly pointed out that we should adhere to the principle of stability and seek progress while maintaining stability, stressed the strengthening of various policy coordination and cooperation, and made a series of deployments such as “accelerating the construction of a modern industrial system”, “focusing on strengthening weak links in the industrial chain” and “vigorously developing the digital economy”.
The year 2023 is the first year to fully implement the spirit of the Party’s 20 National Congress, and it is of great significance to do economic work well. How to promote steady industrial growth? How to enhance the core competitiveness of manufacturing industry? Minister of Industry and Information Technology Jin Zhuanglong recently accepted an interview with Xinhua News Agency
We have the confidence, conditions and ability to promote the steady recovery of the industrial economy
Q: What was the performance of the industrial economy in the past year? How to promote stable industrial growth in 2023?
A: Over the past year, we have worked with various regions and departments to actively respond to the impact of unexpected factors, implement a package of policies to stabilize the economy, and promptly introduce a series of measures to boost the industrial economy. From January to November 2022, China’s industrial added value above designated size increased by 3.8% year-on-year, continuing to play the role of “ballast” for industrial stability of the macroeconomic market.
It is undeniable that the operation of the industrial economy still faces difficulties and challenges, but it should be noted that the advantages of a complete industrial system and a strong domestic market are prominent. In 2023, the combination of optimized epidemic prevention and control measures, stock policies and incremental policies will greatly boost market confidence. We have the confidence, conditions and ability to promote the steady recovery of the industrial economy.
The Ministry of Industry and Information Technology will increase efforts to stabilize growth, strengthen the coordination and cooperation of various policies, and focus on four aspects of work:
First, we strengthened the supply and implementation of policies to stabilize growth. Strengthen the coordination of departments and the linkage of ministries and provinces, implement the policies and follow-up measures that have been issued, strengthen the monitoring and scheduling of industrial economic operation, situation research and judgment, and policy reserves, and introduce more policies and measures in a timely manner.
Second, focus on key industries and regions to stabilize the basic plate of industrial growth. For pillar industries such as machinery, petrochemicals, light industry, automobiles, and electronics, we will study and formulate measures to stabilize growth on a section-by-sector basis. We will create more new growth areas for emerging industries such as new energy, new materials, next-generation information technology, and high-end equipment. We will support the major industrial provinces in taking up the leading role, and support all regions in leveraging their respective strengths and achieving their growth targets.
Third, fully implement the “14th Five-Year Plan” series of plans to boost effective investment in manufacturing. For identified major projects, major projects, major projects, and major projects, start implementation as soon as possible to form a physical workload. We will support manufacturing enterprises to increase investment in high-end, intelligent, and green development, and strengthen service guarantees for major foreign-invested projects in the manufacturing industry.
Fourth, we will actively expand consumption and create new demand with high-quality supply. We will implement the project of new energy vehicles leading the way and developing a strong foundation, and carry out trials for access to intelligent and connected vehicles. We will further implement the “Increase variety, improve quality, and create brands” campaign, promote the movement of green smart home appliances and green building materials to the countryside, vigorously cultivate demonstration cities for information consumption, and promote the development of new technologies, new products, and new models.
Forging long boards, reinforcing short boards, strengthening foundations, and comprehensively upgrading the modernization level of the industrial system
Q: The Central Economic Work Conference emphasized speeding up the construction of a modern industrial system. What specific measures will the Ministry of Industry and Information Technology take?
A: To build a modern industrial system, the key lies in revitalizing the manufacturing industry. We will forge long boards, strengthen weak boards, strengthen the foundation, and comprehensively modernize the industrial system. We will focus on the following five areas:
First, we will improve the autonomy and controllability of key industrial chains. We will identify the weak links in key core technologies and components, carry out key core technology research projects, improve market mechanisms such as “revealing-list”, and take solid steps to strengthen chains and stabilize chains. We will pool high-quality resources to tackle key problems.
Second, we will deepen the reconstruction of the industrial base. Focusing on core basic components, core basic components, key basic materials, key basic software, advanced basic processes and industrial technology foundations, vigorously implementing industrial basic reconstruction projects, laying out a number of common industrial basic technology centers in key areas, and cultivating a number of national manufacturing innovation centers, and actively giving play to the role of key laboratories. Strive to break through a number of key urgently needed basic products.
Third, we will consolidate our leading position in competitive industries. We will accelerate the construction of new infrastructure such as 5G, deepen the integrated application of “5G+ Industrial Internet”, and promote the research and development of 6G technology. Strengthen the new energy automobile industry, comprehensively enhance the competitiveness of the photovoltaic industry, and promote the high-quality development of the shipbuilding industry.
Fourth, we will vigorously transform and upgrade traditional industries. Cultivate a group of leading enterprises with resource control and international competitiveness, vigorously promote technological transformation and equipment upgrading of enterprises, in-depth implementation of intelligent manufacturing projects, comprehensive implementation of green manufacturing, and forge new industrial competitive advantages.
Fifth, we will accelerate the cultivation and growth of emerging industries. We will accelerate the innovation and development of strategic emerging industries such as artificial intelligence, biofuturing, and the Internet of Things, implement special actions for the development of advanced manufacturing clusters, study and formulate action plans for future industrial development, and accelerate the planning and layout of future industries such as humanoid robots, meta-universe, and quantum technology.
We will step up rescue assistance to stabilize market expectations and boost business confidence
Q: In 2023, what new measures will be taken to help enterprises rescue, and how will expectations be stabilized and confidence strengthened?
A: In response to many unexpected factors, China promptly introduced a series of policy measures to relieve difficulties. With the support of various pro-enterprise policies, the majority of small and medium-sized enterprises have been constantly striving to overcome difficulties, showing strong resilience and vitality.
At present, the difficulties and challenges of the stable development of small and medium-sized enterprises are still relatively large, and the Ministry of Industry and Information Technology will further strengthen the policy of benefiting enterprises, the environment of enterprises, the service of enterprises, the innovation of enterprises, and the talent of enterprises, and make every effort to promote the high-quality development of small and medium-sized enterprises.
Specifically, it includes continuously optimizing the development environment, improving the regulations and policies system for small and medium-sized enterprises, continuously carrying out environmental assessment and comprehensive supervision of small and medium-sized enterprises development, and carrying out special actions to reduce the burden on enterprises. We will increase assistance and support, coordinate and promote the continuation and improvement of phased pro-business policies, and introduce a number of measures to help micro, small and medium-sized enterprises maintain steady growth, adjust their structure, and strengthen their capabilities. We will promote the development of specialized and specialized new enterprises, and strive to have more than 80,000 specialized and specialized new small and medium-sized enterprises and more than 10,000 “small giant” enterprises nationwide by the end of 2023. Build a high-quality and efficient service system, and improve the service system for small and medium-sized enterprises at the national, provincial, city and county levels; We will strengthen international exchanges and cooperation, build a number of cooperation zones for small and medium-sized enterprises, improve the overseas service system for small and medium-sized enterprises, and help them “go global”.
We will consolidate the foundation and expand applications, and accelerate the integration of the digital economy and the real economy
Q: What specific measures will the Ministry of Industry and Information Technology take to vigorously develop the digital economy?
A: The digital economy is an important engine driving China’s economic growth and an important advantage in building a modern industrial system. China has built the world’s largest and most technologically advanced network infrastructure, with 2.28 million 5G base stations and gigabit optical networks capable of covering 500 million households. The industrial Internet has been widely integrated into 45 national economic categories, and the role of the digital economy in empowering the real economy has become increasingly prominent.
In 2023, we will thoroughly implement the decisions and arrangements of the Party Central Committee and The State Council, focus on digital technology innovation breakthroughs and application expansion, and promote the deep integration of the digital economy and the real economy.
First, accelerate the construction of digital infrastructure. We will deepen the construction of 5G and gigabit optical networks, coordinate the construction of new infrastructure such as data centers and the industrial Internet, and accelerate the deployment and application of the Internet of vehicles. We will carry out the “Broadband Frontier” special action, and give strong support to the construction of “double gigabit” networks in areas with demand and conditions.
Second, we will promote the innovative development of the digital industry. Focus on key areas such as integrated circuits, 5G, and new displays, and improve the supply of basic hardware and software, core electronic components, key basic materials, and intelligent manufacturing equipment. We will study and formulate supporting policies to better leverage the role of data factors and build world-class digital industrial clusters.
Third, we will deepen industrial digital transformation. Carry out digital transformation actions in the manufacturing industry, promote the popularization of the industrial Internet to industrial parks, build a number of 5G fully connected factories, build a number of global leading smart factories and smart supply chains, and promote the scenario and standardization of small and medium-sized enterprises.
Fourth, we will strengthen network and data security. We will strengthen capacity building for security protection of network infrastructure, establish norms and standards for data security in the industrial and information technology fields, and enhance security capabilities in new convergence areas such as 5G, the industrial Internet, and the Internet of vehicles.
Fifth, improve the environment for the development of the digital economy. Innovate telecom market supervision, guide and urge the compliance development of platform enterprises, deepen the comprehensive management of the network environment such as preventing and cracking down on telecom network fraud, and comprehensively strengthen the protection of users’ rights and interests.
First! 500 MW impact hydropower unit ball valve cast steel shipped
On November 18, the world’s first 500MW impact hydropower unit ball valve cast independently developed by National Machinery Reloading was successfully shipped in Deyang, Sichuan Province. The ball valve cast steel is responsible for the second equipment of the National Machinery Reassembly Institute, and will be applied to the first major technical equipment project (set) in the national energy field developed by Dongfang Electric Power Station – 500 MW impact hydropower unit of Zara hydropower Station.
This is another key component of high-quality major technical equipment created by National Machinery Reinstallation after providing the world’s first 500MW rotary center body forged steel for Zala hydropower Station, marking that National Machinery Reinstallation has become the world’s first enterprise with the core casting and forging manufacturing capability of 500MW impact hydropower units. Han Xiaojun, Secretary of the Party Committee and Chairman of the National Machinery Heavy Loading Party, Yan Zhiyong, Secretary of the Party Committee and chairman of Dongfang Electric Group Dongfang Electric Co., LTD. (referred to as Dongfang Electric) attended the delivery ceremony and delivered a speech. Company leaders Wang Huiqiu, Jiang Tao attended the delivery ceremony.
Han Xiaojun said that National Machinery Reloading and Dongfang Electric are same-city enterprises, but also compatriots, and have always maintained a good strategic cooperative relationship. From the successful development of 500 MW rotary wheel center body forged steel parts in 2023 to the 500 MW ball valve cast steel parts in 2024, both sides are sincere cooperation, work together, implement the spirit of the Third Plenary Session of the 20th CPC Central Committee with the latest achievements in scientific and technological innovation, and actively cultivate and develop new quality productivity. It is a milestone breakthrough in promoting the development of high head and large capacity impact hydropower units in China, and has great significance for the construction of major national hydropower projects in the future and the realization of the national “double carbon” goal.
yan Zhiyong said that after 6 months of unremitting efforts, National Machinery successfully developed the ball valve casting of Zara project, which achieved another “zero” breakthrough in the field of hydropower equipment in China, marking that the development level of China’s hydropower super large impact wheel unit ball valve casting steel has reached a new level. As one of the most core components of high head and large capacity impact hydropower units, the ball valve cast steel is a “super switch” for the safety of impact hydropower units, and will be equipped with the world’s first 500 MW high head impact hydropower generator set independently developed in China. The project will fill the technical gap of China’s giant impact unit and has extremely important demonstration significance.
Over the years, the two sides have focused on accelerating the realization of self-reliance and self-improvement in high-level science and technology, focused on cultivating and developing new quality productive forces, continued to strengthen research on key core technologies, enabled high-quality development through scientific and technological innovation, and jointly provided strong support and guarantee for the construction of major national projects. In the future, the two sides will firmly shoulder the responsibility of “major countries”, work together to support the construction of major national projects, and make greater contributions to ensuring national energy security.
Ball valve casting is the core component of impact hydropower unit, 500 MW Zhala ball valve casting by large valve body, small valve body, valve casting, parts of the maximum weight of about 90 tons, the maximum outline size of more than 5 meters, size specifications, weight are the same type of ball valve most, product quality requirements have reached the highest standards in the industry. As the main supplier of casting and forging parts in the field of domestic energy equipment, in the development process of 500 MW ball valve casting, Guoji Heavy Machinery has broken through the technical bottlenecks such as internal quality assurance of ultra-large wall thick ball valve casting parts, ultra-large specifications and ultra-precision dimension control, and high-performance carbon manganese steel structure precision regulation. Successfully mastered the key core technology of the whole process of the development of 500 MW impact ball valve casting steel parts, and cast excellent quality by lean control of the whole process, and the performance indicators of the products have met the design requirements, and realized the high-quality development of ball valve casting steel parts.
Zhala Hydropower Station has the characteristics of high head, large capacity and high altitude, which is a supporting demonstration project to realize the localization of independent intellectual property rights of the whole industrial chain of impact hydropower generating units and improve the development capacity of high-drop hydropower resources in China.