Open die forging finds applications in various industries where high-strength and durable metal components are required. The versatility and flexibility of the open die forging process make it suitable for a wide range of applications.
Open die forging application
Aerospace: Open die forging is extensively used in the aerospace industry to produce critical components such as turbine discs, compressor shafts, landing gear parts, engine components, and structural elements. The process ensures high strength, reliability, and performance required for aircraft applications.
Automotive: Open die forging plays a crucial role in the automotive industry. It is used to manufacture components like crankshafts, connecting rods, axle shafts, gears, suspension parts, and steering knuckles. Open die forging provides superior strength, fatigue resistance, and dimensional accuracy for demanding automotive applications.
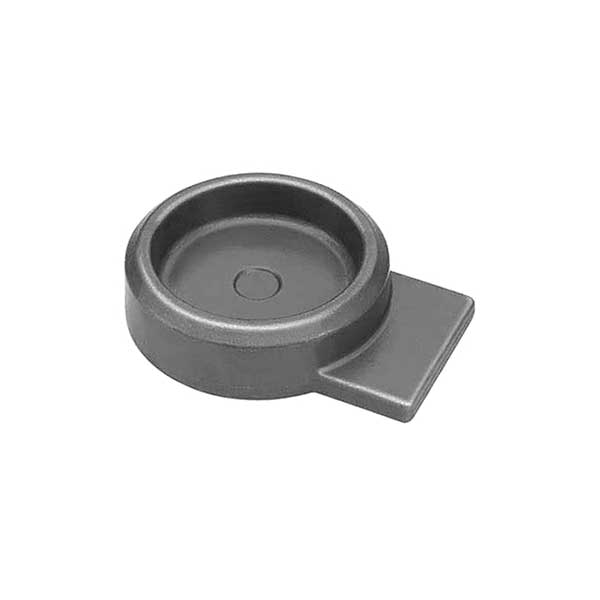
Oil and Gas: In the oil and gas sector, open die forging is employed to produce components for exploration, drilling, and production equipment. This includes drill bits, valves, wellhead components, flanges, and pipeline fittings. Open die forging ensures the required strength, toughness, and resistance to harsh operating conditions in the oil and gas industry.
Power Generation: Open die forging is used in the power generation industry for the production of turbine shafts, generator rotors, and other critical components in steam turbines, gas turbines, and hydroelectric generators. The process ensures the necessary strength, reliability, and dimensional precision required for power generation applications.
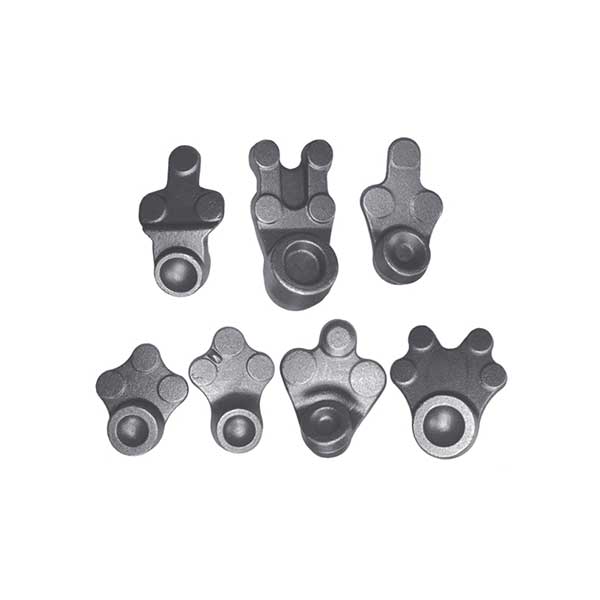
Mining and Construction: Open die forging finds applications in the mining and construction sectors for manufacturing components like heavy machinery parts, excavator tracks, gears, couplings, and high-strength fasteners. Open die forging provides the durability and resistance to heavy loads and harsh operating environments.
Defense and Military: Open die forging is utilized in the defense and military sectors for the production of critical components such as artillery shells, tank parts, missile components, and armored vehicle components. The process ensures the required strength, impact resistance, and structural integrity for military applications.
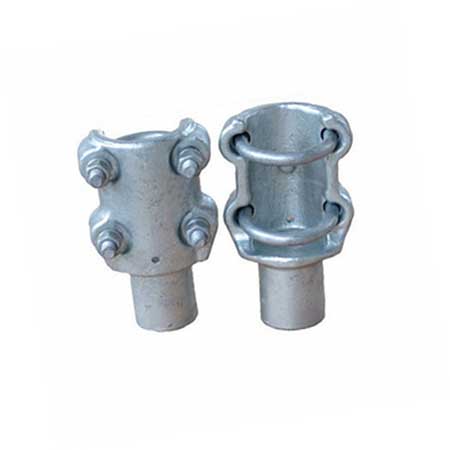
Heavy Machinery and Equipment: Open die forging is employed in the manufacturing of various heavy machinery and equipment components, including gears, crankshafts, bearing rings, and industrial tooling. The process provides high strength, durability, and dimensional accuracy for heavy-duty applications.
General Engineering: Open die forging finds applications in general engineering industries for producing a wide range of components requiring strength, durability, and precise dimensions. This includes shafts, flanges, fittings, rods, and customized parts for diverse engineering applications.
These are just some of the many application fields where open die forging is employed. The process is versatile and adaptable, allowing for the production of components in various shapes, sizes, and materials to meet specific industry requirements.
What are the advantages of closed die forging
Closed die forging, also known as impression die forging, is a metal forming process in which heated metal is shaped within a closed set of dies to achieve the desired final shape. This process offers several advantages that make it a preferred choice for producing certain types of metal components.
Closed die forging advantages
High Precision and Accuracy: Closed die forging allows for the production of highly precise and accurate metal components. The closed dies constrain the material’s flow, resulting in tight tolerances and consistent dimensions.
Excellent Material Integrity: The closed die forging process subjects the material to controlled deformation, leading to improved grain structure, reduced porosity, and enhanced material integrity. This results in better mechanical properties, including increased strength and fatigue resistance.
Enhanced Mechanical Properties: The controlled deformation and grain flow during closed die forging result in superior mechanical properties compared to other manufacturing methods. The directional grain flow leads to enhanced strength, toughness, and durability of the finished parts.
Reduced Material Waste: Closed die forging involves minimal material waste since the metal is shaped within the closed dies. This efficient material usage contributes to cost savings and reduced environmental impact.
Wide Material Compatibility: Closed die forging can be performed with a wide range of materials, including various metals and alloys such as steel, aluminum, titanium, and more. This versatility allows for the production of components with diverse material properties.
Complex Shapes and Designs: Closed die forging can accommodate complex part geometries and intricate designs that might be challenging to achieve with other manufacturing processes. The dies can be designed to create intricate features, undercuts, and fine details.
Improved Surface Finish: The closed die forging process generally results in parts with a better surface finish compared to some other metal forming methods. This can reduce the need for additional machining or finishing operations.
Cost Efficiency: While the initial tooling and die setup costs can be higher than some other processes, closed die forging offers long-term cost savings due to its high material utilization, reduced scrap rates, and enhanced mechanical properties, which can lead to longer component lifetimes.
Batch Production and High Volume Capability: Closed die forging is well-suited for batch production and high-volume manufacturing. Once the dies are created and set up, the process can be repeated consistently to produce large quantities of identical parts.
Environmental Benefits: Closed die forging’s material efficiency and reduced waste generation contribute to its environmental benefits. The process aligns with sustainability goals by minimizing material consumption and energy usage.
Closed die forging is commonly used to produce a wide range of components, from small intricate parts to larger and more robust components used in various industries, including automotive, aerospace, construction, energy, and more. The process’s advantages make it a preferred choice for producing components that require high precision, strength, and reliability.
What are the benefits of open die forging?
Open die forging, also known as free forging, is a metalworking process where a workpiece is hammered or pressed between two flat dies or anvils. The dies do not enclose the entire workpiece, allowing the metal to flow laterally and shape the material. This forging method offers several benefits, making it suitable for various applications. Some of the key benefits of open die forging include:
Customizable Shapes: Open die forging allows for the creation of custom shapes and sizes, making it suitable for producing large, non-standard, or unique components that may be difficult or impractical to manufacture using other methods.
Improved Mechanical Properties: The forging process aligns the grain structure of the metal, resulting in improved mechanical properties, including higher strength, better toughness, and improved fatigue resistance. This makes open die forged parts well-suited for critical applications in industries such as aerospace, oil and gas, and automotive.
Reduced Material Waste: Open die forging can be highly material-efficient since it typically involves minimal machining or material removal compared to other manufacturing processes. This reduces material waste and contributes to cost-effectiveness.
Enhanced Structural Integrity: The absence of seams or joints in open die forged parts leads to enhanced structural integrity and better reliability, especially in applications subjected to high stress or extreme conditions.
Cost-Effective for Low-Volume Production: Open die forging can be economically viable for low-volume production runs or one-off components due to its simplicity and minimal tooling requirements.
Short Lead Times: The open die forging process usually has shorter lead times compared to some other metalworking methods, making it suitable for time-sensitive projects.
Versatility: Open die forging can be used with various metals and alloys, including carbon steels, stainless steels, aluminum, titanium, and nickel-based alloys, allowing for a wide range of applications across different industries.
No Size Limitations: Since the workpiece is not confined within a closed die, open die forging can accommodate large or oversized components, making it ideal for forging parts such as shafts, cylinders, and large machinery components.
Improved Grain Flow: The working of the metal during open die forging promotes directional grain flow, leading to improved mechanical properties and better performance of the final product.
While open die forging offers numerous benefits, it is important to note that the process may not provide the same level of precision or complexity achievable through closed-die forging or other advanced shaping methods. The selection of the forging method should be based on the specific requirements of the component, cost considerations, and production volume.
What are the types of closed die forging
Closed die forging, also known as impression-die forging, is a metalworking process where metal is shaped by compressive forces applied through the use of specially designed dies. There are several types of closed die forging techniques, each suitable for different applications and shapes.
Types of closed die forging
Upsetting
In this type of closed die forging, the length of the workpiece is reduced while its cross-sectional area is increased. The metal is compressed between the upper and lower dies, causing the material to flow outward and thicken. Upsetting is often used to create heads, caps, and similar components.
Cogging
Cogging is a preliminary forging operation used to reduce the overall size of the workpiece. It involves repeated heating and forging to gradually shape the metal into a rough form, making it easier to handle and further process.
Blocking
In blocking, the workpiece is shaped into a rough outline of the final desired product. This process usually requires several dies to progressively deform the metal into a more defined shape. Blocking is often followed by other forging operations to achieve the final product’s details.
Coining
Coining is a closed die forging process used to create intricate and precise features on the workpiece’s surface. It involves high pressures to imprint patterns, designs, or letters onto the metal.
Fullering
Fullering is a forging operation that creates grooves or channels on the workpiece’s surface. It is commonly used to produce handles, decorative elements, or to facilitate further shaping processes.
Bending
In bending, the workpiece is deformed to achieve a specific curvature or bend. Multiple die sets are typically used to progressively bend the metal to the desired shape.
Edging
Edging is a closed die forging operation used to create flanges or edges on the workpiece. It involves localized compression to produce the desired edge configuration.
Extrusion
In this type of closed die forging, the metal is forced through a die to produce elongated shapes with a consistent cross-section. Extrusion is often used to create rods, tubes, or other linear components.
Swaging
Swaging is a process used to reduce the diameter of a cylindrical workpiece by applying radial compressive forces through the use of dies. It is commonly employed to create tapered shapes or to reduce the diameter of a rod.
Each of these closed die forging techniques has its advantages and is selected based on the specific requirements of the final product. Closed die forging is widely used in various industries to produce high-strength, durable, and complex metal components used in machinery, automotive, aerospace, and other applications.
What are the steps of closed die forging process
Closed die forging, also known as impression die forging, is a metal forging process in which heated metal is shaped within a set of dies to produce a near-net-shape or final component. The process involves several steps to transform the raw material into the desired forged product.
The steps of closed die forging
Billet Heating
The raw material, usually a metal billet, is heated in a furnace to an appropriate forging temperature. The temperature is specific to the type of metal being forged and is crucial for achieving proper plasticity and reducing the risk of cracking during the forging process.
Die Preparation
The dies, which consist of an upper and lower die set, are prepared and mounted in the forging press or hammer. The dies are precision machined to create the desired shape and features of the final forged component.
Billet Placement
The heated billet is placed in the lower die, which has a cavity that matches the desired shape of the final product.
Closing and Forming
The upper die is brought down to close the dies and apply pressure to the billet. The force exerted by the forging press or hammer shapes the billet within the die cavity. The material flows and fills the cavities in the die, taking the shape of the final product.
Flash Formation
As the dies close, excess material, known as flash, is squeezed out between the die halves. The flash acts as a reservoir, helping to ensure complete filling of the die cavity and maintaining the desired shape of the forged component.
Ejection
After the forming operation, the dies are opened, and the forged part is ejected from the die cavity. Any excess flash is trimmed or removed.
Heat Treatment and Finishing
The forged component may undergo heat treatment processes such as quenching, tempering, or annealing to achieve the desired material properties. Additional finishing operations, such as machining, grinding, or surface treatments, may be performed to meet the final specifications and requirements of the component.
It’s important to note that the closed die forging process can be modified depending on the complexity of the component being forged and the specific requirements of the application. Additionally, the process may involve multiple forging steps or operations to achieve the final shape and properties of the forged component.
What are the features of forged wheels
A forged wheel is a type of wheel that is manufactured through a forging process. Forging is a manufacturing method where a solid piece of metal is shaped and formed under high pressure and heat to create the desired wheel shape.
Here are some key features and benefits of forged wheels:
Strength and Durability
Forged wheels are known for their superior strength and durability. The forging process compacts the metal structure, aligns the grain flow, and eliminates any weak points or porosity, resulting in a wheel that can withstand high loads, impacts, and stress. This makes forged wheels highly resistant to bending, cracking, and deformation.
Weight Reduction
Forged wheels offer weight savings compared to other wheel manufacturing methods, such as cast wheels. The forging process allows for precise shaping and thinning of the wheel’s walls, reducing unnecessary material without compromising strength. The reduced weight contributes to improved acceleration, braking, and overall vehicle performance.
Enhanced Performance
The combination of strength and weight reduction in forged wheels translates into improved performance characteristics. The reduced unsprung weight contributes to better handling, responsiveness, and suspension performance. Additionally, the increased strength allows for better energy transfer, minimizing power loss and maximizing efficiency.
Customization
Forged wheels offer a wide range of customization options in terms of design, finish, and size. The forging process allows for intricate designs and complex shapes to be created, giving customers the opportunity to personalize their wheels and match their vehicle’s aesthetics.
Heat Dissipation
Forged wheels have better heat dissipation properties compared to other wheel types. The compacted metal structure and improved surface area-to-volume ratio help dissipate heat generated during braking, reducing the risk of brake fade and prolonging the life of braking components.
Quality and Craftsmanship
Forged wheels are often associated with high-quality craftsmanship and attention to detail. The forging process requires skilled labor and precise control, resulting in wheels with superior surface finish, dimensional accuracy, and overall quality.
Exclusive and High-End Applications
Due to their superior strength, durability, and aesthetic appeal, forged wheels are commonly used in high-performance and luxury vehicles. They are often considered a premium option and are favored by automotive enthusiasts who seek top-of-the-line components for their vehicles.
It’s worth noting that the cost of forged wheels is generally higher compared to other wheel types due to the complex manufacturing process and the use of high-quality materials. However, the benefits in terms of performance, durability, and customization options make
What is the ring forging process
Ring forging is a manufacturing process used to produce seamless rings with desired dimensions and properties. It involves the shaping of metal through localized compressive forces applied to a heated workpiece. Here is an overview of the ring forging process:
Material Selection: The process begins with selecting the appropriate material for the desired ring. Common materials used in ring forging include carbon steel, alloy steel, stainless steel, and various non-ferrous metals.
Billet Heating: The selected material is heated to a specific temperature range, typically above its recrystallization temperature, to improve its plasticity and make it easier to shape. Heating can be done in furnaces or using induction heating methods.
Preforming: Once the billet reaches the desired temperature, it is placed on a die and subjected to an initial shaping process. Preforming can be performed using various techniques, such as open die forging, closed die forging, or rolling.
Ring Rolling: The preformed billet is then moved to a ring rolling machine, which consists of two or more rotating rolls. The rolls exert pressure on the billet to deform it into the desired ring shape. The process is typically conducted at elevated temperatures to reduce the forging forces and enhance material flow.
Ring Expansion: If necessary, the ring may be subjected to additional expansion processes, such as mandrel expansion or radial-axial rolling, to achieve the desired dimensions, thickness, and contour.
Heat Treatment: After the ring is formed, it undergoes heat treatment processes, such as annealing, normalizing, or quenching and tempering, to improve its mechanical properties, hardness, and strength.
Finishing Operations: The forged ring may undergo additional processes to remove scale, surface defects, or irregularities. These operations can include machining, grinding, or shot blasting to achieve the final desired finish.
Inspection and Testing: The finished ring is subjected to various quality control measures, including dimensional inspections, non-destructive testing (such as ultrasonic or magnetic particle testing), and mechanical property testing to ensure it meets the required specifications and standards.
Ring forging can produce rings of various sizes and complexities, ranging from small precision rings to large industrial components. The process offers several advantages, including improved mechanical properties, enhanced structural integrity, and cost-effectiveness compared to other manufacturing methods.
It’s important to note that the specifics of the ring forging process may vary depending on factors such as the material, size, and complexity of the ring being produced, as well as the equipment and techniques employed by the forging facility.
What are the application fields of open die forging
Open die forging finds applications in various industries where high-strength and durable metal components are required. The versatility and flexibility of the open die forging process make it suitable for a wide range of applications.
Open die forging application
Aerospace: Open die forging is extensively used in the aerospace industry to produce critical components such as turbine discs, compressor shafts, landing gear parts, engine components, and structural elements. The process ensures high strength, reliability, and performance required for aircraft applications.
Automotive: Open die forging plays a crucial role in the automotive industry. It is used to manufacture components like crankshafts, connecting rods, axle shafts, gears, suspension parts, and steering knuckles. Open die forging provides superior strength, fatigue resistance, and dimensional accuracy for demanding automotive applications.
Oil and Gas: In the oil and gas sector, open die forging is employed to produce components for exploration, drilling, and production equipment. This includes drill bits, valves, wellhead components, flanges, and pipeline fittings. Open die forging ensures the required strength, toughness, and resistance to harsh operating conditions in the oil and gas industry.
Power Generation: Open die forging is used in the power generation industry for the production of turbine shafts, generator rotors, and other critical components in steam turbines, gas turbines, and hydroelectric generators. The process ensures the necessary strength, reliability, and dimensional precision required for power generation applications.
Mining and Construction: Open die forging finds applications in the mining and construction sectors for manufacturing components like heavy machinery parts, excavator tracks, gears, couplings, and high-strength fasteners. Open die forging provides the durability and resistance to heavy loads and harsh operating environments.
Defense and Military: Open die forging is utilized in the defense and military sectors for the production of critical components such as artillery shells, tank parts, missile components, and armored vehicle components. The process ensures the required strength, impact resistance, and structural integrity for military applications.
Heavy Machinery and Equipment: Open die forging is employed in the manufacturing of various heavy machinery and equipment components, including gears, crankshafts, bearing rings, and industrial tooling. The process provides high strength, durability, and dimensional accuracy for heavy-duty applications.
General Engineering: Open die forging finds applications in general engineering industries for producing a wide range of components requiring strength, durability, and precise dimensions. This includes shafts, flanges, fittings, rods, and customized parts for diverse engineering applications.
These are just some of the many application fields where open die forging is employed. The process is versatile and adaptable, allowing for the production of components in various shapes, sizes, and materials to meet specific industry requirements.
What is included in the forging design system
When discussing the composition of a forging design system, it is important to clarify that the term “forging” typically refers to a metalworking process, and it may not directly relate to a design system in the context of software or user interfaces. However, if you are referring to a design system specifically tailored for the forging industry, the composition may include the following elements:
Design Principles
Establishing design principles specific to the forging industry can guide the overall visual and interaction design decisions. These principles may focus on safety, efficiency, ergonomic considerations, and adherence to industry standards.
Visual Style
Defining a visual style guide for the forging design system helps ensure a consistent and visually appealing user interface. This may involve selecting appropriate colors, typography, iconography, and other visual elements that align with the industry’s aesthetics and brand identity.
Component Library
Building a component library specifically designed for the forging industry allows for efficient and consistent development of user interfaces. This library may include specialized components for displaying and interacting with forging-related data, such as temperature controls, pressure gauges, tool selection, or material properties.
Interaction Patterns
Developing interaction patterns tailored to the forging industry helps designers and developers create intuitive user interfaces. These patterns may include workflows for forging processes, task-driven navigation, error handling, and feedback mechanisms that align with the specific needs of forging applications.
Accessibility
Prioritizing accessibility is crucial in any design system, including one for the forging industry. Ensuring that the user interfaces are accessible to individuals with disabilities by adhering to relevant accessibility standards is essential.
Documentation and Guidelines
Creating comprehensive documentation and guidelines assists designers and developers in understanding and implementing the forging design system effectively. This documentation should cover design principles, component usage, coding standards, and specific considerations related to the forging industry.
Collaboration and Feedback
Establishing channels for collaboration and feedback among designers, developers, and industry experts enables continuous improvement and refinement of the forging design system. This collaboration helps ensure that the system meets the unique needs and requirements of the forging industry.
It’s worth noting that the specific composition of a forging design system may vary depending on the scope and goals of the system, as well as the specific requirements and processes of the forging industry.
What is hot forging used for?
Hot forging is a manufacturing process that involves shaping metal using heat and pressure. It is commonly used in various industries for a wide range of applications. Here are some common uses of hot forging:
Automotive Industry
Hot forging is extensively used in the automotive industry to manufacture critical components such as crankshafts, connecting rods, gears, axles, and suspension parts. The process provides high strength and durability to the forged components, making them suitable for demanding automotive applications.
Aerospace Industry
The aerospace industry relies on hot forging to produce components that require high strength, precise dimensions, and resistance to extreme conditions. Forged aerospace parts include turbine blades, landing gear components, engine parts, and structural components.
Oil and Gas Industry
Hot forging is utilized in the oil and gas industry for the production of various equipment and components, including valves, flanges, fittings, drill bits, and downhole tools. These components require excellent mechanical properties, resistance to corrosion, and the ability to withstand high-pressure and high-temperature conditions.
Heavy Machinery and Equipment
Hot forging is employed in the manufacturing of heavy machinery and equipment components such as gears, crankshafts, hydraulic cylinder rods, and construction machinery parts. The process ensures the necessary strength, durability, and dimensional accuracy of these components.
Power Generation
Hot forging is used in the power generation industry for the production of turbine blades, generator shafts, and other critical components. These components need to withstand high temperatures, pressure differentials, and mechanical stresses.
Tool and Die Industry
Hot forging is utilized to produce tool and die components such as dies, punches, molds, and inserts. These components require high wear resistance, toughness, and dimensional accuracy to withstand the rigors of metalworking processes.
General Engineering
Hot forging finds application in various general engineering sectors, including agricultural machinery, mining equipment, industrial machinery, and infrastructure projects. It is used to manufacture components that require high strength, toughness, and dimensional stability.
Hot forging offers several advantages, including improved material properties, enhanced mechanical strength, better structural integrity, and cost-effectiveness for large production runs. The process allows for the shaping of metals into complex shapes with high precision and repeatability.
What is the forged shaft process
The shaft forging process is a manufacturing method used to produce shafts with superior strength, durability, and reliability. It involves shaping and forming a solid metal billet into the desired shaft shape through the application of heat and pressure.
Shaft forging process
Billet Preparation: The process begins with the selection of a suitable metal billet, typically made of steel or other alloy materials. The billet should have sufficient dimensions to accommodate the final shaft shape.
Heating: The billet is heated in a furnace to a temperature above its recrystallization temperature but below its melting point. This temperature allows the metal to become more malleable and facilitates deformation during the forging process.
Forming: Once the billet reaches the desired temperature, it is transferred to a forging press or hammer. There are two primary forging methods used for shaft production:
a. Open-Die Forging: In open-die forging, the heated billet is placed on a stationary anvil, and repeated blows from a hammer or press deform the metal into the desired shape. The operator guides the deformation by moving the billet between strikes to achieve the desired dimensions.
b. Closed-Die Forging: Closed-die forging involves placing the heated billet between two die halves that contain the desired shape. The dies are then brought together, applying pressure to the billet and forcing it to take the shape of the die cavities. This method provides more precise control over the final shape of the shaft.
Finishing Operations: After the initial forging, the shaft may undergo various finishing operations to refine its shape and dimensions. These operations can include trimming excess material, machining critical features, drilling holes, or grinding the surface to achieve the desired finish.
Heat Treatment: Once the shaft has been formed and finished, it may undergo heat treatment processes such as annealing, quenching, or tempering to enhance its mechanical properties, such as strength, hardness, and toughness. The specific heat treatment process depends on the material composition and desired properties of the shaft.
Inspection and Testing: Quality control measures, including non-destructive testing techniques, are employed to ensure the integrity and reliability of the forged shaft. These inspections may include visual examination, dimensional checks, ultrasonic testing, magnetic particle inspection, or other methods to identify any defects or abnormalities.
Machining and Surface Treatment: If necessary, the forged shaft may undergo additional machining processes, such as turning, milling, or grinding, to achieve precise dimensions or desired surface characteristics. Surface treatments such as coating, plating, or painting may also be applied for corrosion resistance or aesthetic purposes.
By following these steps, the shaft forging process can produce high-quality shafts with improved mechanical properties compared to other manufacturing methods. The resulting shafts exhibit excellent strength, fatigue resistance, and structural integrity, making them suitable for various applications across industries such as automotive, aerospace, machinery, and more.