Carburized steel 20CrMnTi forgings are air-cooled to room temperature after forging to obtain a mixed structure composed of ferrite, pearlite, Widmansite and bainite. After heating to 930°C for carburizing and cooling to 850°C for quenching, coarse austenites still appear. Body grains, showing obvious tissue heredity. If after forging, after heat treatment, a mixed structure of ferrite and pearlite is obtained, after carburizing and quenching, the structure is obviously refined, and there is no organization heredity, which is the significance of heat treatment after forging. The main purposes of heat treatment for small gear forgings are:
(1) Eliminate forging stress.
(2) Obtain a relatively uniform metallographic structure and improve cutting performance.
(3) Reduce the deformation of the gear after carburizing and quenching.
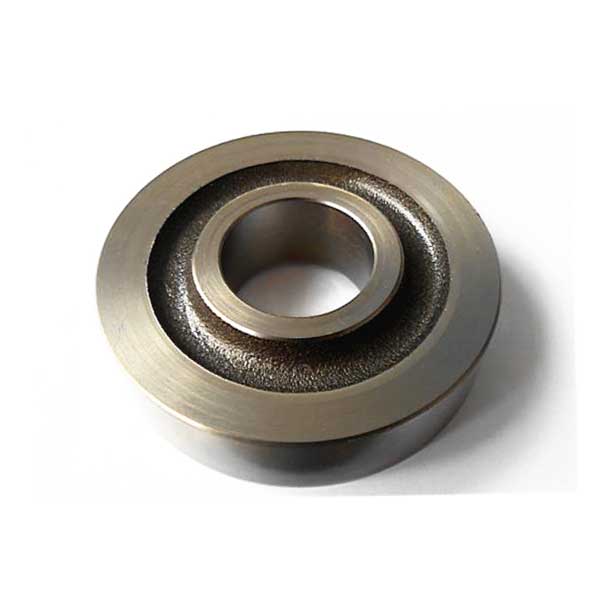
1. Isothermal annealing
The forging material is 20CrMnTi, and the equipment is an isothermal annealing continuous furnace, which consists of a high temperature zone, a rapid cooling zone and an isothermal zone.
The isothermal annealing process is an advanced high-temperature heating zone for forgings. It is heated from room temperature to 940°C and held for a period of time to make it fully austenitized. Then it enters the rapid cooling zone and is rapidly cooled from 950°C to 650°C within 5~10 minutes. Make the forgings quickly enter the correct phase transformation range, and then keep warm at 650°C to make the forgings fully phase-transform to ferrite + pearlite structure, and send them out of the furnace to air cool to room temperature.
It should be noted that due to the different sizes of forgings, the isothermal annealing process curve should be adjusted according to the actual situation of the production site. The principle is to ensure that the metallographic structure of forgings is 1~3, and the surface hardness is preferably controlled at 160~210HBW. After testing, this production process is also suitable for the annealing of small shaft forgings, and the production capacity of the equipment is 600kg/h.
2. Waste heat annealing
The forging material is 20CrMnTi, and the equipment is a mesh belt waste heat annealing furnace, which is composed of a heating furnace and a rapid cooling chamber. The preheating annealing process is that after the forging is formed, it is directly sent into the heating furnace, kept at 650°C for 45 minutes, and then enters the rapid cooling room, and is cooled to below 70°C within 20 minutes.
When annealing with residual heat of forgings, the key point is to grasp the temperature of forgings entering the furnace and the holding time in the furnace. After field tests, it is found that the temperature of general forgings entering the furnace should be controlled above 800°C. At this time, the metallographic phase and hardness after annealing are most suitable; Forgings below 800℃ are likely to have unqualified microstructure and hardness after annealing with residual heat, so strict attention should be paid to them. The holding time and temperature cannot be generalized, and should be adjusted appropriately according to the size and thickness of the forging.
3. Comparison of isothermal annealing and waste heat annealing
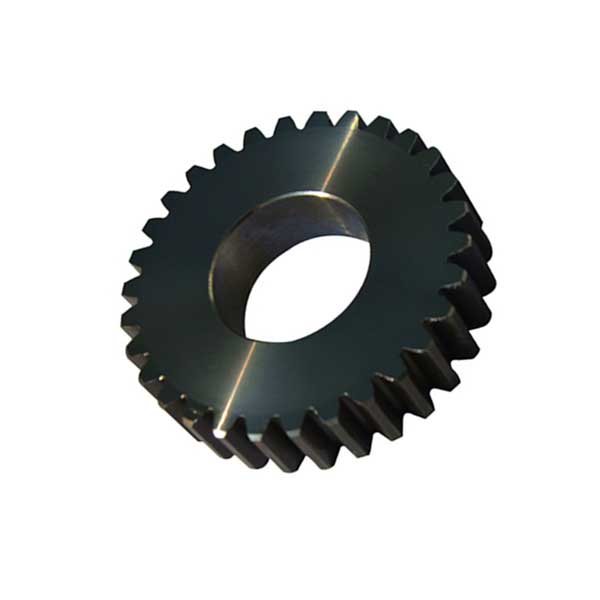
(1) Isothermal annealing process
Advantage:
a. The process stability is high, and the dispersion of forging hardness can be controlled within 20HBW/batch. The whole annealing process is easy to control, and the metallographic structure and surface hardness of the forgings after annealing can meet the requirements, and it is also the most widely used heat treatment method for forgings at present.
b. Because it is independent from the forging production line and does not interact with other forging equipment’s mobility, it will neither stop the furnace due to the failure of a certain equipment, nor stop the forging production line due to the abnormality of the isothermal annealing line.
Disadvantages:
a. After the forging is completely cooled, reheat it to about 940°C, which will cause energy waste.
b. The isothermal annealing line cannot be incorporated into the forging production line to realize the “one-flow” forging production mode.
Therefore, it is necessary to set up a special store for normalizing goods, and wait for the amount of forgings to meet the production capacity of the isothermal annealing equipment before they are put into the furnace. Such an intermediate goods store will occupy a large amount of site resources and current assets, which does not meet the “0” intermediate storage in the Toyota production method. thought of.
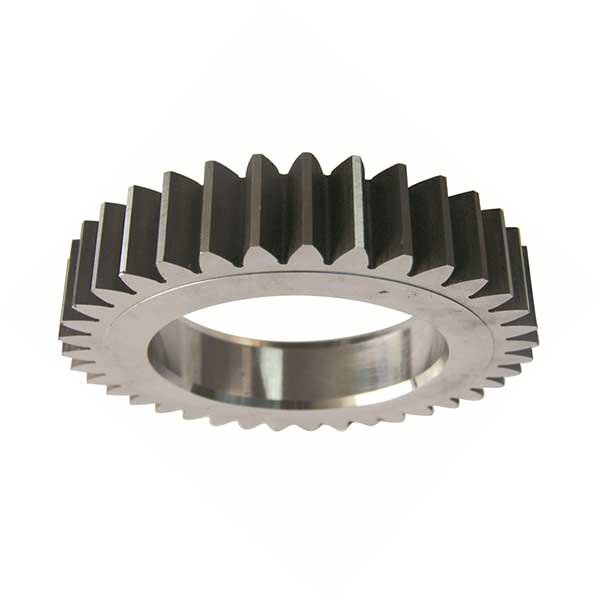
(2) Waste heat annealing process
Advantage:
a. Energy saving and environmental protection are in line with the low-carbon economy advocated by our country. It uses the waste heat of forgings, saves the heating process, and its energy consumption can be reduced to 50% of that of general isothermal annealing.
b. Combined with the forging production line, it saves the site resources and working capital occupied by the warehouse in the middle.
Disadvantage:
a. Although the residual heat annealing process has been proven to be reliable and has been widely used in production, due to the different forging equipment and the different operating speeds of forging operators, it is relatively difficult to control the furnace entering temperature, which is easy to cause tissue damage. Unqualified hardness.
b. It must follow each forging production line and interact with the mobility of other forging equipment, that is to say, any failure of the waste heat annealing furnace or any equipment of this forging production line will directly cause the entire production line to stop production.
c. Because the heating and cooling process of the annealing furnace is time-consuming and power-consuming, the forging production line matched with the waste heat annealing is preferably a saturated production line with three shifts, and at least two shifts must be ensured. Otherwise, the production is 8 hours and the empty furnace is running for 16 hours. of.
The above is the relevant introduction about the annealing heat treatment process of small gear forgings. You can comprehensively measure the quality, cost, delivery time, site and other factors of actual production, and choose a suitable forging annealing process.
What are the application fields of hot forging
Hot forging is a metalworking process that involves heating a metal above its recrystallization temperature and then shaping it through compressive force. This process is commonly used in a wide range of industries to create various components and parts. Here are some of the application fields of hot forging:
Automotive: Hot forging is widely used in the automotive industry to produce components such as crankshafts, connecting rods, and gears. These parts are essential for the proper functioning of engines and other critical systems in vehicles.
1. Aerospace: Hot forging is also used in the aerospace industry to produce various parts such as turbine blades, landing gear components, and structural parts for aircraft.
2. Industrial machinery: Hot forging is used in the production of various components for industrial machinery such as hydraulic cylinders, gear blanks, and crankshafts.
3. Construction: Hot forging is used in the construction industry to produce components such as bolts, nuts, and other fasteners that are essential for building structures.
4. Oil and gas: Hot forging is used in the oil and gas industry to produce various components such as valves, flanges, and piping fittings that are used in pipelines, refineries, and other facilities.
5. Military and defense: Hot forging is also used in the military and defense industries to produce components such as missile and bomb casings, tank parts, and other critical components.
In summary, hot forging is a widely used metalworking process that is used in a variety of industries to produce various components and parts. It is commonly used in the automotive, aerospace, industrial machinery, construction, oil and gas, and military and defense industries, among others. The high strength, durability, and precision of hot forged parts make them essential for many critical applications.
How to choose a forging manufacturer
When choosing a forging manufacturer, it is important to consider several key factors to ensure that you select a reputable and capable company that can meet your needs. Here are some key factors to consider:
Experience and Expertise: Look for a forging manufacturer with a proven track record of delivering high-quality forgings and experience in the industry. Consider their expertise in the specific type of forging you require and ask about their history of producing similar products.
Quality Control: A manufacturer with a strong commitment to quality control is important in ensuring the forgings you receive meet your specifications and requirements. Ask about their quality control processes, including material inspection and testing, and review their quality control certificates, such as ISO 9001.
Capabilities: Consider the manufacturer’s capabilities, including the types of forging processes they offer, the size of forgings they can produce, and the materials they can work with. A manufacturer with a range of capabilities is more likely to be able to meet your needs.
Equipment and Technology: Ask about the manufacturer’s equipment and technology, and whether they have the latest technology to ensure high-quality, efficient production.
Lead Time and Delivery: Consider the manufacturer’s lead time and delivery schedule, and whether they can meet your required delivery timeline. A manufacturer that can offer quick turnaround times can be a major advantage.
Cost: Price is an important factor to consider, but it should not be the only factor. It is important to balance cost with quality and reliability, and to select a manufacturer that offers a competitive price while still meeting your needs and requirements.
Reputation and Reliability: Research the manufacturer’s reputation, including customer reviews and feedback, to get a better understanding of their reliability and customer satisfaction. You can also ask for references and talk to other companies that have used their services.
In conclusion, choosing the right forging manufacturer is important to ensure that you receive high-quality forgings that meet your needs and requirements. Consider the above factors to make an informed decision and select a manufacturer that will provide you with the best value for your investment.
Introduction of closed die forging process
Closed die forging is a metal forming process in which a billet or preform is placed between two dies, which are then brought together under high pressure to shape the material into the desired form. The dies are typically made of hardened steel and are machined to have a precise shape, so that the finished product has a high degree of accuracy and repeatability. The term “closed die” refers to the fact that the billet is fully enclosed within the dies and cannot move or escape during the forging process.
The process of closed die forging typically involves several stages, including preheating the billet to a temperature that is suitable for forging, placing the billet in the dies, and applying pressure to shape the billet. The pressure is typically applied using a forging press or hammer, and the final shape of the product is determined by the shape of the dies.
Closed die forging offers several advantages over other metal forming processes, including higher strength and toughness, improved dimensional accuracy, and the ability to produce complex shapes. It is commonly used in the manufacture of components for various industries, such as automotive, aerospace, and construction.
Closed die forging is commonly used in the manufacture of a wide range of components, including gears, shafts, valves, and other components for various industries, such as automotive, aerospace, and construction. The process offers several advantages over other metal forming processes, including higher strength and toughness, improved dimensional accuracy, and the ability to produce complex shapes. Additionally, closed die forging can be used to produce parts with a high degree of detail, such as small ribs or intricate patterns.
What are the characteristics of multi-directional die forging process?
Multi-directional die forging is a precision forging technology that performs split-die forging on a multi-directional die forging hydraulic press, and its deformation is mainly extrusion. During multi-directional die forging, two or more punches (or punch cores) pressurize the bad material simultaneously or sequentially from different directions for extrusion or upsetting.
Compared with ordinary die forging and split die forging, multi-directional die forging has the characteristics of simple structure and long service life. Forgings such as class, cylindrical parts, large valve bodies, pipe joints, aircraft landing gear, engine casings, disc shaft assemblies, etc. have begun to be produced by multi-directional die forging technology. Combined with the application of multi-directional die forging, we have made a detailed summary of the process characteristics of multi-directional die forging, let’s understand it together.
Multi-directional die forging process characteristics
1. The material utilization rate is high. Compared with the open die forging, there is no waste of flash material. The shape of the forging can be designed to be hollow, and the forging slope of the punching hole can be canceled or reduced, thereby saving 30%-50% of metal.
2. The performance of the forging is good. Since the shape of most forgings is formed by die forging, the fiber structure is distributed along the contour of the forging, so the mechanical properties of the forging are good, and the general strength can be increased by more than 30%.
3. It is suitable for the forming of high alloy steel and special alloy. Because the blank is deformed under three-dimensional compressive stress during forging, its process plasticity is improved, which greatly facilitates the forming of high alloy and special alloy materials with poor plasticity and narrow forging temperature range. take shape.
4. High productivity. Compared with ordinary die forging, the number of working steps can generally be reduced by 50%, so the forging time is greatly reduced and the production efficiency is greatly improved.
5. Wide applicability, can be used for hollow frames of various alloys, solid and hollow branch forgings, fork forgings, cylindrical parts, various valve bodies, pipe joints and shaft forgings.
Multi-directional die forging belongs to closed die forging, and the forgings have no flash, and more internal shapes of forgings can be obtained by forging. Therefore, it is required to have high blanking precision, and at the same time, it is required to use less and no oxidation heating. In addition, multi-directional die forging requires a special multi-directional die forging hydraulic press with good rigidity and high precision or a special die forging device with complex structure attached to the general equipment.
Technical requirements for forged shaft forgings
Shaft forgings should choose different materials and adopt different heat treatment specifications (such as quenching and tempering, normalizing, quenching, etc.) according to different working conditions and use requirements, in order to obtain certain strength, toughness and wear resistance.
45 steel is a commonly used material for shaft forgings. It is cheap and can obtain better cutting performance after quenching and tempering (or normalizing), and can obtain comprehensive mechanical properties such as higher strength and toughness. The surface hardness after quenching can be improved. Up to 45~52HRC.
Alloy structural steel such as 40Cr is suitable for shaft forgings with medium precision and high rotational speed. This kind of steel has good comprehensive mechanical properties after quenching and tempering.
Bearing steel GCr15 and spring steel 65Mn, after quenching and tempering and surface high-frequency quenching. The surface hardness can reach 50~58HRC and has high fatigue resistance and good wear resistance, and can manufacture high-precision shafts.
38CrMoAIA nitrided steel can be used for the main shaft of precision machine tools (such as the grinding wheel shaft of grinding machine and the main shaft of coordinate boring machine). After quenching and tempering and surface nitriding, this kind of steel can not only obtain high surface hardness, but also maintain a soft core, so it has good impact resistance and toughness. Compared with carburizing and quenching steel, it has the characteristics of small heat treatment deformation and higher hardness.
Shaft forgings are one of the typical forgings often encountered in machines. It is mainly used to support transmission parts, transmit torque and bear load. Shaft forgings are rotating body forgings whose length is greater than the diameter and are generally composed of outer cylindrical surfaces, conical surfaces, inner holes, threads and corresponding end surfaces of concentric shafts. According to different structural shapes, shaft forgings can be divided into optical shafts, stepped shafts, hollow shafts and crankshafts. A shaft with an aspect ratio of less than 5 is called a short shaft, and one with an aspect ratio greater than 20 is called a slender shaft, and most shafts are in between.
The shaft is supported by bearings, and the shaft section that fits with the bearing is called the journal. The journal is the assembly benchmark of the shaft. Their accuracy and surface quality are generally required to be high. The technical requirements are generally formulated according to the main function and working conditions of the shaft. Usually, there are the following items:
Geometric shape accuracy: The geometric shape accuracy of shaft forgings mainly refers to the roundness and cylindricity of the journal, outer tapered surface, Morse taper hole, etc., and its tolerance should generally be limited within the dimensional tolerance range. For inner and outer circular surfaces with high precision requirements, the allowable deviation should be marked on the drawing.
Dimensional accuracy: In order to determine the position of the shaft, the journal that acts as a support usually requires high dimensional accuracy (IT5~IT7). The dimensional accuracy of the journal of the assembled transmission parts is generally lower (IT6~IT9).
Mutual position accuracy: The position accuracy requirements of shaft forgings are mainly determined by the position and function of the shaft in the machine. Generally, the coaxiality requirements of the shaft journal for assembling the transmission part to the supporting shaft journal should be guaranteed, otherwise the transmission accuracy of the transmission part (gear, etc.) will be affected and noise will be generated. For ordinary precision shafts, the radial runout of the matching shaft section to the supporting journal is generally 0.01~0.03mm, and for high-precision shafts (such as spindles), it is usually 0.001~0.005mm.
Shaft forgings can be in the form of bars, forgings and other rough forms according to the use requirements, production type, equipment conditions and structure. For shafts with little difference in outer diameter, bar is generally the main material; for stepped shafts or important shafts with large difference in outer diameter, forgings are often used, which not only saves materials but also reduces the workload of machining. Improve mechanical properties.
According to the different production scales, there are two forging methods for blanks: free forging and die forging. Free forging is mostly used in small and medium batch production, and die forging is used in mass production.
Detailed explanation of gear forging annealing heat treatment process
Carburized steel 20CrMnTi forgings are air-cooled to room temperature after forging to obtain a mixed structure composed of ferrite, pearlite, Widmansite and bainite. After heating to 930°C for carburizing and cooling to 850°C for quenching, coarse austenites still appear. Body grains, showing obvious tissue heredity. If after forging, after heat treatment, a mixed structure of ferrite and pearlite is obtained, after carburizing and quenching, the structure is obviously refined, and there is no organization heredity, which is the significance of heat treatment after forging. The main purposes of heat treatment for small gear forgings are:
(1) Eliminate forging stress.
(2) Obtain a relatively uniform metallographic structure and improve cutting performance.
(3) Reduce the deformation of the gear after carburizing and quenching.
1. Isothermal annealing
The forging material is 20CrMnTi, and the equipment is an isothermal annealing continuous furnace, which consists of a high temperature zone, a rapid cooling zone and an isothermal zone.
The isothermal annealing process is an advanced high-temperature heating zone for forgings. It is heated from room temperature to 940°C and held for a period of time to make it fully austenitized. Then it enters the rapid cooling zone and is rapidly cooled from 950°C to 650°C within 5~10 minutes. Make the forgings quickly enter the correct phase transformation range, and then keep warm at 650°C to make the forgings fully phase-transform to ferrite + pearlite structure, and send them out of the furnace to air cool to room temperature.
It should be noted that due to the different sizes of forgings, the isothermal annealing process curve should be adjusted according to the actual situation of the production site. The principle is to ensure that the metallographic structure of forgings is 1~3, and the surface hardness is preferably controlled at 160~210HBW. After testing, this production process is also suitable for the annealing of small shaft forgings, and the production capacity of the equipment is 600kg/h.
2. Waste heat annealing
The forging material is 20CrMnTi, and the equipment is a mesh belt waste heat annealing furnace, which is composed of a heating furnace and a rapid cooling chamber. The preheating annealing process is that after the forging is formed, it is directly sent into the heating furnace, kept at 650°C for 45 minutes, and then enters the rapid cooling room, and is cooled to below 70°C within 20 minutes.
When annealing with residual heat of forgings, the key point is to grasp the temperature of forgings entering the furnace and the holding time in the furnace. After field tests, it is found that the temperature of general forgings entering the furnace should be controlled above 800°C. At this time, the metallographic phase and hardness after annealing are most suitable; Forgings below 800℃ are likely to have unqualified microstructure and hardness after annealing with residual heat, so strict attention should be paid to them. The holding time and temperature cannot be generalized, and should be adjusted appropriately according to the size and thickness of the forging.
3. Comparison of isothermal annealing and waste heat annealing
(1) Isothermal annealing process
Advantage:
a. The process stability is high, and the dispersion of forging hardness can be controlled within 20HBW/batch. The whole annealing process is easy to control, and the metallographic structure and surface hardness of the forgings after annealing can meet the requirements, and it is also the most widely used heat treatment method for forgings at present.
b. Because it is independent from the forging production line and does not interact with other forging equipment’s mobility, it will neither stop the furnace due to the failure of a certain equipment, nor stop the forging production line due to the abnormality of the isothermal annealing line.
Disadvantages:
a. After the forging is completely cooled, reheat it to about 940°C, which will cause energy waste.
b. The isothermal annealing line cannot be incorporated into the forging production line to realize the “one-flow” forging production mode.
Therefore, it is necessary to set up a special store for normalizing goods, and wait for the amount of forgings to meet the production capacity of the isothermal annealing equipment before they are put into the furnace. Such an intermediate goods store will occupy a large amount of site resources and current assets, which does not meet the “0” intermediate storage in the Toyota production method. thought of.
(2) Waste heat annealing process
Advantage:
a. Energy saving and environmental protection are in line with the low-carbon economy advocated by our country. It uses the waste heat of forgings, saves the heating process, and its energy consumption can be reduced to 50% of that of general isothermal annealing.
b. Combined with the forging production line, it saves the site resources and working capital occupied by the warehouse in the middle.
Disadvantage:
a. Although the residual heat annealing process has been proven to be reliable and has been widely used in production, due to the different forging equipment and the different operating speeds of forging operators, it is relatively difficult to control the furnace entering temperature, which is easy to cause tissue damage. Unqualified hardness.
b. It must follow each forging production line and interact with the mobility of other forging equipment, that is to say, any failure of the waste heat annealing furnace or any equipment of this forging production line will directly cause the entire production line to stop production.
c. Because the heating and cooling process of the annealing furnace is time-consuming and power-consuming, the forging production line matched with the waste heat annealing is preferably a saturated production line with three shifts, and at least two shifts must be ensured. Otherwise, the production is 8 hours and the empty furnace is running for 16 hours. of.
The above is the relevant introduction about the annealing heat treatment process of small gear forgings. You can comprehensively measure the quality, cost, delivery time, site and other factors of actual production, and choose a suitable forging annealing process.
Analysis of technical characteristics of forged shaft forgings
Forging is a processing method that uses forging machinery to apply pressure to metal blanks to cause plastic deformation to obtain shaft forgings with certain mechanical properties, certain shapes and sizes. Forging and stamping belong to the nature of plastic processing, collectively referred to as forging. Forging is a common forming method in mechanical manufacturing. The as-cast looseness and welding holes of the metal can be eliminated by forging, and the mechanical properties of forgings are generally better than castings of the same material. For important parts with high load and severe working conditions in machinery, forgings are mostly used except for plates, profiles or weldments that can be rolled with simple shapes.
The recrystallization temperature of steel is about 460°C, but 800°C is generally used as the dividing line, and hot forging is above 800°C; it is called warm forging or semi-hot forging between 300 and 800°C.
Forging can be divided into cold forging and hot forging according to the temperature of the blank during processing. Cold forging is generally processed at room temperature, and hot forging is processed at a temperature higher than the recrystallization temperature of the blank metal. Sometimes it is also called warm forging when it is heated but the temperature does not exceed the recrystallization temperature. However, this division is not completely uniform in production.
According to the forming method, forging can be divided into free forging, die forging, cold heading, radial forging, extrusion, forming rolling, roll forging, rolling and so on. The deformation of the billet under pressure is basically not subject to external restrictions, which is called free forging, also known as open forging; the deformation of the billet in other forging methods is restricted by the mold, which is called closed mode forging. There is a relative rotational movement between the forming tools of forming rolling, roll forging, rolling, etc. and the blank, and the blank is pressed and formed point by point and gradually, so it is also called rotary forging.
Generally, round or square bars are used as blanks for small and medium-sized shaft forgings. The grain structure and mechanical properties of the bar are uniform and good, the shape and size are accurate, the surface quality is good, and it is convenient to organize mass production. As long as the heating temperature and deformation conditions are controlled reasonably, shaft forgings with excellent performance can be forged without large forging deformation.
Forging materials are mainly carbon steel and alloy steel with various components, followed by aluminum, magnesium, copper, titanium and their alloys. The original state of the material is bar stock, ingot, metal powder and liquid metal.
How to determine the forging process plan?
The purpose of economic analysis of forging processing is to explore technical solutions and pursue economic effects. Any production process must not only formulate the process, determine the process parameters and process equipment, but also discuss the economic effect.
The principle of determining the forging process is to create the most material wealth with less labor consumption. The optimization of the process is to find the minimum value in the total consumption of materials, equipment, energy and labor under the premise of ensuring product quality and quantity. For the forging process, it can be specifically: high dimensional accuracy of forgings, organization and performance meeting requirements; less raw material consumption, small equipment investment, simple tools, low energy consumption, low labor intensity, and no environmental pollution.
Techno-economic effects are carried out using the comparative method. When comparing process schemes, there may be more than two schemes. In order to make the analysis conclusion correct, an exhaustive method should be used to list possible schemes or alternative schemes. To this end, it is necessary to carry out forging process analysis, explore a variety of processes and schemes, and prepare conditions for technical and economic analysis and selection of process schemes. The tasks of general process analysis can be summarized as follows: according to the functional characteristics, materials, shapes, dimensional accuracy, quality requirements and production batches of parts, in the existing or available equipment, devices, tools, energy, inspection methods, management level and personnel Under the condition of quality, put forward various process schemes that can be used.
When conducting a process analysis, the following questions must be considered and answered:
(1) Whether it can meet the function of the forging;
(2) Whether it can meet the technical requirements of drawings and quality standards;
(3) Whether the structure of the forging is reasonable and whether there is any excess dressing;
(4) Whether the residual collision can be reduced;
(5) Whether the deformation force or deformation function is reduced;
(6) Whether the metal streamline meets the requirements;
(7) Whether there are any omissions in the quality assurance process;
(8) Whether the processes and steps have been minimized;
(9) Whether the material is fully utilized, and whether it is possible to forge with other parts together, with multiple pieces in one mold or multiple pieces in one blank;
(10) Have you considered cold forging, precision forging, rolling, partial die forging, segmented die forging, combined die forging, forging and welding, etc.?
According to the shape, size and deformation mode of the forging, calculate the deformation force, and select the main forging equipment. Determine the heating temperature according to the forging material and deformation method, and select the heating method and heating equipment. The blanking equipment is selected according to the type of forging equipment, the deformation method and the size of the blank. Determine the process route according to the quality requirements of the forgings, and select equipment such as trimming, calibration, tip pressure, heat treatment, cleaning, inspection, and flaw detection. Determine the production takt and productivity according to the production batch, and then calculate the number of equipment generations. According to equipment performance characteristics and productivity, calculate various consumption data, such as material, power, blanking, auxiliary material and mold consumption. According to the selected process, consider the production organization, equipment characteristics, determine the plant area required for production and the number of production workers, auxiliary workers, technical and management personnel. Then analyze the advantages and disadvantages of various processes, such as: labor conditions, environmental protection and its technical and labor skills needs.
Process analysis is a systematic engineering problem, so people who are engaged in this work are required to be familiar with the existing production methods, and master the characteristics, application scope and constraints of various process schemes. Can correctly calculate various technical parameters, understand the current situation, trends and development trends of forging production at home and abroad, and can infer and predict according to actual conditions.
What is the difference between hot forging and cold forging?
Forging transforms metal workpieces by compression at cold, hot or hot temperatures. Cold forging increases the strength of a metal by hardening it at room temperature. Hot forging achieves optimum yield strength, low hardness, and high ductility by hardening the metal at extremely high temperatures. Whether to use hot or cold forging depends on the function, industry and production volume of the finished part.
The difference between hot forging and cold forging
While cold forging compresses metal at room temperature, hot forging requires high temperatures. The main difference between cold forging and hot forging is that the high temperature of hot forging gives the metal a finer and more complex shape than cold forging.
Hot forging
The hot forging temperature varies depending on the metal type. Hot forging begins by heating the die to prevent any temperature loss during the process and to ensure that crystallization does not occur until the forming is complete. Heating makes the metal more ductile. When the pressure of the die squeezes the hot metal, the structure transforms into finer grains, which increase yield strength and ductility.
Factors to consider when hot forging include:
Cool down
If the metal cools to a temperature below the minimum threshold, the forging is complete. If this happens before reaching the final shape, the metal must be reheated.
Tolerance
The dimensional tolerances of hot forging are not as precise as cold forging.
Specification
Hot forging dies are customized according to customer’s part specifications.
Cold forging
Cold forging uses a displacement process to shape the material into the desired shape. The compressive force squeezes the metal between the punch and die at room temperature until the material conforms to the contour of the die. Cold forging techniques include rolling, pressing, drawing, spinning, upsetting and extrusion.
Factors to consider when cold forging include:
Material volume
Careful control of material volume prevents stress and damage, especially in closed forging, as excess material has nowhere to escape.
Bonding
This coating process improves material flow during the process to reduce forces, stresses and friction while improving surface quality.
Annealing
Annealing softens metal and improves material flow. It can be applied as an intermediate process when work hardening occurs before the forging process is completed.
Lubricating
Lubrication is critical in the cold forging process. High-viscosity oil prevents metal-to-metal friction, and thin oil dissipates heat.
Advantages and disadvantages of hot forging and cold forging
Advantages of hot and cold forging
Hot forging adds ductility to more complex parts and allows for more customization options; cold forging produces no waste, requires little finishing, maintains dimensional accuracy, and produces high surface quality.
Disadvantages of hot and cold forging:
Additional cost of hot forging heat treatment, less precise dimensional tolerances, risk of warpage; cold forging has few custom options, risk of residual stress, may require heat treatment.
The above is about the process difference between hot forging and cold forging. When choosing which forging process to use, you must understand its characteristics in advance.
Detailed explanation of cold forging forming process
Cold forging is a general term for plastic processing such as cold die forging, cold extrusion, and cold heading. It is the forming process of the material below the recrystallization temperature, and the forging is carried out below the recovery temperature. In production, forging without heating the blank is called cold forging.
Most of the cold forging materials are aluminum and some alloys, copper and some alloys, low carbon steel, medium carbon steel, and low alloy structural steel with low deformation resistance and good plasticity at room temperature. Cold forgings have good surface quality and high dimensional accuracy, which can replace some cutting processes. Cold forging can strengthen the metal and increase the strength of the part.
Introduction of cold forging process
Cold precision forging is a (near) net shape forming process. The parts formed by this method have high strength and precision and good surface quality. At present, the total amount of cold forgings used in an ordinary car abroad is 40~45kg, of which the total amount of toothed parts is more than 10kg. The single-piece weight of cold forged gears can reach more than 1kg, and the tooth shape accuracy can reach 7 grades.
Continuous process innovation has promoted the development of cold extrusion technology. Since the 1980s, domestic and foreign precision forging experts have begun to apply the split forging theory to the cold forging of spur and helical gears. The main principle of shunt forging is to establish a shunt cavity or shunt channel of material in the forming part of the blank or die.
During the forging process, while the material fills the cavity, part of the material flows to the shunt cavity or shunt channel. The application of shunt forging technology enables the less and no cutting processing of higher precision gears to quickly reach an industrial scale. For extruded parts with a length-diameter ratio of 5, such as piston pins, cold extrusion can be achieved at one time by axial shunt by using a wide range of axial residual blocks, and the stability of the punch is very good; for flat spur gears Forming, the use of radial residual blocks can also achieve cold extrusion forming of products.
Blocked forging is to extrude metal in one or two directions through one or two punches in a closed die at one time to obtain near-net shape precision forgings without flash. If some car precision parts such as planetary and half shaft gears, star sleeves, cross bearings, etc. are processed by cutting, not only the material utilization rate is very low (less than 40% on average), but also it takes a lot of man-hours and the production cost is extremely high. These net shape forgings are produced in foreign countries using occlusion forging technology, which saves most of the cutting process and greatly reduces the cost.
Advantages and disadvantages of cold forging
Cold forging process is a precision plastic forming technology, which has unparalleled advantages of cutting, such as good mechanical properties, high productivity and high material utilization rate of products, especially suitable for mass production, and can be used as a manufacturing method for final products. , It has a wide range of applications in industries such as transportation, aerospace and machine tool industries.
Material requirements are high; not suitable for small amounts of processing; mold requirements are high.
The above is a detailed introduction to the cold forging process. The forming accuracy of cold forging technology is higher than that of warm forging and hot forging, and it has its unique advantages in the field of precision forming. The application of the cold forging process improves the bore finish, dimensional accuracy and surface strength, prolongs the life of the barrel, and improves the shooting accuracy of the gun accordingly, and it is easy to process the tapered barrel and reduce the quality.